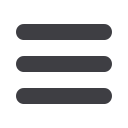

result, the challenge is passed on to
the circuit level. Initially to the circuit’s
analog-front-end, and subsequently
to digital signal processors. Available
analog IPs are generic, maybe
programmable to some extent, but
not co-designed with the sensor
and the reference circuits that are
required at system level. As a result,
the traditional analog IP buy-in model
where a set of IPs is glued together
in a chip will result in a sub-optimal
system. Instead of working with
standard component analog IP, a
much better approach is to work with
proven topologies (whose functionality
is already proven in silicon) and fine-
tune them for the application’s sweet
spot.
A last and equally essential aspect
that the new hardware hipsters have
covered is electrostatic discharge
(ESD), electrical overstress (EOS) and
latch-up. Bart Keppens from Sofics
says that what he has learned by
supporting innovative startups is that
many of the applications require non-
standard on-chip ESD/EOS protection
clamps, which are not always covered
in mass-produced designs. “For
example, the driving voltage of the
implanted chip to restore hearing for
(near) deaf people is in the order of
20V, much beyond the typical I/O
interfaces provided by the foundry or
I/O providers. Similarly, small signals
(order of a few mV or mA) captured
by sensors for motion detection and
touch remain hidden in the noise or
are lost due to leakage. Moreover,
the probability of ESD stress is much
higher as they are operated in harsh
environments. For example, the plastic
of your smartphone cover rubbing
on the cloth of your back-pocket
can generate very high voltages just
millimeters away from very sensitive
components, such as high-speed USB
ports.”
Enabling low-cost
prototyping and small-
volume production
For substream innovators, unlike
for larger companies, achieving the
lowest possible unit production cost
is not the first concern. They can
reduce the production unit cost later
on, once the product is on the market
and customers turn out to buy more
products than anticipated. Their
game plan centers on producing truly
innovative and high-margin products
for niche markets, with the potential
to grow into larger, more mature
markets.
Instead, when a startup or an
innovative SME implements an IoT
product involving a custom chip
design, the go/no-go decision is
typically taken by private or venture
capital investors and dominated
by the required amount of upfront
investment (NRE cost), the time-to-
market, and the ability to precisely
define the chip’s requirements.
“That is where IC-link and its design
partners may help,” says Ramses
Valvekens. “They can help lower the
NRE costs and shorten the time to
market through their extensive IP and
know-how. In addition, together with
the customer, they will help define
and focus the chip requirements.”
One essential factor included in
the NRE is the initial cost of the
lithographic mask set needed to
process the wafers. These can cost,
even for mature technologies, in
the range of 100,000s of dollars.
Especially to lower these high
NRE cost for SMEs, foundries have
introduced multi-project wafers
(MPWs) and made these accessible
through partners such as imec IC-
link. In MPWs, designs of many
customers share space on the same
mask, but with hard limits imposed
on the maximum number of chips per
wafer, and the total number of wafers
that can be ordered. For very small
production runs measured in the
thousands, mature MPW technologies
offer extremely low initial costs, as
low as 10,000s of dollars for a batch
of approximately 100 prototypes of
32 mm2. Below figure illustrates the
impact that MPW processing has on
small volume production, as well as
the change in the cost model when
higher production volumes require a
transition to a dedicated mask.
Substream innovation is
here to stay
The convergence of high-growth,
fragmented, wirelessly connected
application domains characterized
by manufacturing sweet spots using
mature technologies has led to an
explosion of activity by SMEs. New
product ideas can be generated by
small teams of people and taken
quickly to small volume production
and are no longer only the domain
of large international corporations.
Imec IC-link and its partners have
committed to support this process, by
providing infrastructure, design and
IP assistance.
23 l New-Tech Magazine Europe