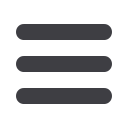

102
N
ovember
2011
www.read-tpt.com›
A
rticle
Dimensional tolerances lower than ½ of that specified by the
Standards are achieved (Tables 3 to 5).
The required standard tolerances EN 10219, EN10217, EN 10296,
EN 10208, EN 10305-3 and API5L are adequately fulfilled.
Besides, special products can be manufactured and special
customers’ requirements met.
The welding quality (Figure 9), which is decisively influenced by the
forming section and the HF generator, allows the welding of critical
sizes and grades.
The tube quality is inspected directly downstream of the welding
table, where the tube is submitted to a 100% check for welding
defects on an ultrasonic tester (Figure 10).
Another important and growing requirement to be satisfied by the
product is the quality of the inside scarfing.
In addition to production quality and yield, the dimension changing
time is an important factor regarding plant efficiency. At present,
about ten wall thickness changes and two diameter changes
(complete changes) per week are performed. On average, a wall
thickness change takes from zero to 15 minutes, depending on the
fact the tube is not inner scarfed. Presently a complete size change
over take approx. 2½ hours with five operators assigned.
Characteristic
The nearest tolerance to:
EN10219 – EN10208 –
EN10217 – ISO3183 – API5L
ASTM A450
EN10305-3
(max thick 6mm)
Example 1
Ø 127. x 12.
S355
Example 2
Ø 323.9 x 16.
S355
Diameter
(body + ends)
± 0.5%
with a min: ± 0.5mm
& max: ± 1.0mm
ends:
Ø ≤ 168.3
min: -0.4mm
Ø 101.6 ÷ 190.5:
-0.64 / +0.38mm
Ø 190.5 ÷ 228.6:
-1.14 / +0.38mm
< Ø 120.: ±0.60
Ø 127. ÷ 139.7.: ±0.80
Ø 159. ÷ 193.7.: ±1.00
126.91 ÷ 127.42 =
0.51mm
323.90 ÷ 324.37 =
0.47mm
Ovality
body
2%
2%
In the tolerance
of the diameter
0.4%
0.14%
ends
1.5%
Straightness
1.5mm/mt on the total length & locally ≤ 3mm on 1mt
< 1.0mm/mt
< 1.0mm/mt
Table 3
:
Dimensional tolerances of round products
Characteristic
EN10219
EN10305-3
(sp max 4mm)
ASTM A500
Example 1
Ø 100. x 100. x8.
S355
Example 2
Ø 300. x 150. x 14.
S355
Example 3
Ø 250. x 250. x 12.
5 S355
Side dimension
H,B<100mm ±1%
with min: ±.5mm ±0.65
Ø ≤63.5: ±0.51mm
63.5<Ø≤88.9: ±0.64mm
88.9<Ø≤139.7: ±0.76mm
Ø>139.7: ±1% of the
greater dimension
(tolerances for
B=H & H<1.5*B)
For: 1.5*B≤H≤3*B :
1.5 tolerance of B
H>3*B : 2.0 tolerance of B
100 ≤ H,B ≤
200mm
±0.8%
±0.70
99.74 ÷ 99.82
99.83 ÷ 100.20
H,B>200mm ±0.6%
/
299.80 ÷ 300.20
149.35 ÷ 149.80
249.75 ÷ 250.10
249.4 ÷ 249.80
Concavity /
convexity
±8.5%
with min 0.5mm
Included into side
dimension tolerances
Included into side
dimension tolerances
0.40mm
0.20mm
0.30mm
Squareness of sides
90° ±1°
90°±1°
90°±2°
90°
90°
90°
Radius of corner
T ≤ 6mm 1.6xT<r≤2.4xT
r≤2.2xT
r≤3.0xT
6<T≤10mm 2.0xT<r≤3.0xT
17.3 ÷ 19.5
(16 ÷ 24)mm
T>10mm 2.4xT<r≤3.6xT
39.3 ÷ 40.5
(33.6 ÷ 50.4)
33 ÷ 36
(30 ÷ 45)
Straightness
1.5mm/mt on the total length & locally ≤ 3.0mm on 1 mt
10.4mm/5*L
< 1.0mm/mt
< 1.5mm/mt
< 1.5mm/mt
Twist
2.0 mm + 0.5mm/mt
Max 3mm/mt
Max 2 ÷ 3mm/mt
< 0.5mm/mt
<0.5mm/mt
<0.5mm/mt
Table 4
:
Dimensional tolerances of square and rectangular products
Figure 9
:
HF-Welding: Ø 139.7 X 9.7 –S355