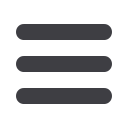

18
N
ovember
2011
www.read-tpt.com›
I
ndustry
N
ews
Intelligent Trench wins prestigious
health and safety award
THE Intelligent Trench underground
mapping solution won the Health & Safety
at Work award at the Chartered Institution of
Highways & Transportation annual awards
ceremony, which took place in June.
Judges for the award, who represent
a variety of stakeholders from across
the industry, were looking for solutions
that demonstrably led to improvements
in health and safety, and which could
in particular show originality, robust
implementation, best value cost-benefit
and wider implementation potential.
By deploying RFID markers in
excavations and collecting data and photo-
graphic evidence about buried apparatus
using GPS enabled PDA software, this
information is thereafter available free of
charge at any time, making future works
safer and more effective. Data can be
obtained during any excavation or as part of
a non-invasive survey.
The Intelligent Trench solution provides
instant access to the data through both a
desktop portal and directly to the field via
supported devices. RFID locators enable
the position of previous works and the
location and depth of buried plant to be
accurately determined, even in built up
areas where techniques such as GPS
often fail. Future works may then benefit
from access to photographs and other
asset data, enabling better compliance
with health and safety guidelines such as
HSG47.
Infotec
– UK
Email:
sales@infotec1.netWebsite:
www.infotec1.netMarshall repositions precision medical
machining services
MARSHALL Manufacturing has announced
the repositioning of its precision machining
services to accommodate a growing need
from medical OEMs who increasingly
outsource
engineering
and
design
assistance responsibility as they downsize
their in-house engineering departments.
Responding
to
these
changes,
Marshall Manufacturing has repositioned
the company as an integrated precision
services solution provider. This includes
a broadened spectrum of design for
manufacturability (DFM), including design
engineering assistance, prototyping, device
validation implementation and precision
manufacturing.
Marshall’s medical speciality is the
process design and manufacturing of high
precision Swiss machined components,
machined needles, 2D and 3D contouring,
and bending of machined wire and tubes.
End-use products include urethral needles
for sling implants, trocars, surgical tools and
spine implants.
Explaining the move, Michael Burchill,
president of Marshall Manufacturing
stated, “Simply being a precision parts
manufacturer in today’s medical device
industry is not enough. We will be making
more of our experience and resources
available to assist customers with the
development and manufacturing of their
products. As the engineering outsourcing
trend has grown, it has been a challenge
and opportunity for our talented staff
to step up and play a greater role in our
medical customers’ innovation.”
“Marshall Manufacturing has been
performing these services for many years
in a less structured way than our new
plans going forward,” Mr Burchill said.
“One example of how we responded to
the new outsourcing trend occurred when
a medical company asked us to develop
a process for 3D contouring an MP35N
tubular component after it had been Swiss
machined. The challenges were many,
but we developed a proprietary process
for making the component that actually
improved the efficacy of the device.”
Another area of increased activity has
come directly from surgeons. “We’ve had
many surgeons approach us seeking
manufacturing assistance for surgical tools
they’ve envisioned,” Mr Burchill reported.
“With little more than their napkin sketch,
we’ve developed workable prototypes,
proceeded into test quantities, and worked
through arduous design change and
acceptance stages and finally into quantity
manufacturing for the medical industry.”
Also driving Marshall Manufacturing’s
repositioning efforts are time-to-market
considerations, difficult to process new
materials and cost reduction pressures.
“Marshall Manufacturing is experienced
in meeting these challenges,” reported
Mr Burchill. “We have a 20-year wealth
of knowledge that we bring to the design
and manufacture of sophisticated metal
surgical instruments and implants. Our
knowledge and experience can bring about
important changes for the better.
“For example, in the medical industry
there is a tendency to specify tighter
tolerances
than
necessary,
which
contributes to higher costs and longer
development times.Another problemarea is
incorrect material selection and processing
techniques. They negatively influence the
contouring of medical tubes and rods for
needles, contributing to productivity losses
and increased costs. We have the skilled
teams and manufacturing resources to do
things better in all of these areas.”
Marshall Manufacturing
– USA
Fax: +1 800 321 6728
Email:
contact@marshallmfg.comWebsite:
www.marshallmfg.comMarshall Manufacturing is an ISO 13485:2003
and ISO 9001:2008 certified manufacturer of
medical components