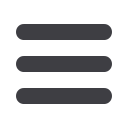

22
N
ovember
2011
www.read-tpt.com›
I
ndustry
N
ews
API certification for Horn
IN spring 2011 Paul Horn GmbH was
assessed as meeting requirements for
certification to API Q1 by the American
Petroleum Institute (API). API is the
leading trade association for the oil and
gas industry whose specifications are
recognised internationally. By meeting the
quality system requirements of API Spec
Q1, companies demonstrate that they are
capable of meeting the industry’s exacting
demands.
Hartmetall-Werkzeugfabrik Paul Horn
GmbH is now listed on the APIQR’s
Composite List. It is thus far the first
manufacturer worldwide of turning and
milling tools to achieve this distinction.
As well as certification according to ISO
9001:2008, Paul Horn GmbH can now
refer to an industry specific, internationally
recognised standard. It may also mark its
products with the API monogram.
Horn tool systems for machining of oil
field pipes and sleeves – such as System
117 – are designed for the end machining
of rotating or stationary oil field pipes up to
25" diameter. The product range currently
includes tools for external and internal
turning of API and special threads, internal
and external chamfering, machining sealing
seats, grooving, parting off and peeling.
Paul Horn GmbH
– Germany
Email:
christian.thiele@phorn.deWebsite:
www.phorn.dePaul Horn has received its
API Q1 certificate
Modernised strip galvanising line
boosts productivity
WUPPERMANN Staal Nederland BV has
placed an order with SMS Elotherm for the
modernisation of a strip galvanising line
delivered in 2000. With an inductive booster
heating system from SMS Elotherm, it is
claimed that Wuppermann will be able to
increase its productivity by 30 per cent.
SMS Elotherm is to supply a complete
3,600kW induction plant with two strip coils.
In addition there will be new components
for the existing plant and the line controller
will be integrated into the overall process.
Erection and commissioning as well as
training of the customer’s personnel also
form part of the order.
With the inductive booster heating at the
tower entry, the ingoing temperature from
the pickling line is raised by approximately
150°C. The existing plant power is then
used to increase the temperature to process
temperature. The efficiency of the booster
heating system will in future be higher
than the values at present. The inductive
booster heating plant for strip galvanising
is designed for strip thicknesses from 0.8 to
4mm and a strip width of up to 1,660mm.
Wuppermann has planned a 15-day
standstill for installation and commissioning.
The start of production after the installation
of the booster heating plant is scheduled for
the beginning of 2012.
SMS Elotherm GmbH
– Germany
Fax: +49 2191 891 229
Email:
info@sms-elotherm.deWebsite:
www.sms-elotherm.com