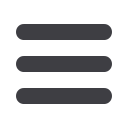

N
ovember
2011
81
›
B
ending
& T
ube
M
anipulation
Leaner, meaner and greener
ADDISONMCKEE’s innovative new
‘Hydra Green’ technology allows its
latest end forming equipment to take
advantage of hydraulic power without the
constant noise, heat and energy usage
associated with traditional hydraulic
power units.
Whereas traditional hydraulic systems
for endforming machines use an AC motor
continuously driving a hydraulic pump
even when the machine is not in use and
no oil pressure and/or flow is required,
AddisonMckee’s new technology is
designed so that the pump is in operation
only when there is a demand for increased
pressure/flow.
In the final analysis, the ‘Hydra Green’
solution, at the heart of the new HG70
range of end formers, will deliver a
number of key benefits over a traditional
hydraulic circuit in terms of using 50 per
cent less electricity due to the significantly
reduced duty cycle of the hydraulic pump,
minimising heat emissions and drastically
reducing noise emissions by as much as
50 per cent. The system also achieves a
major reduction in the amount of hydraulic
maintenance required – while the smaller
hydraulic reservoir uses a remarkable 65
per cent less oil.
The technology’s functionality will also
allow for enhanced machine motion control
by using the variable speed of the servo
pump to control oil flow rate and machine
speed.
And, most importantly, with the system
naturally sitting in a low energy state when
the machine is idle and the pump not
generating pressure or flow, operator safety
is also significantly enhanced.
It’s fair to say that AddisonMckee’s
programme of technological innovation
has two main drivers: cutting unnecessary
emissions by its machines and cutting
costs for its customers. The new eb80
ESRB machine, for example, represents
a significant alternative to the existing
world renowned DB 75 machine but with
significant cost advantages achieved
through removing the ball screw providing
the boost and allowing the gearbox and
motor instead to provide the force required
for boosting, enabling freeform bending for
the full length of the bed.
Not only that but, given the cost of
floorspace at any facility, the new
machine’s modular design also has
significant benefits if bed length flexibility
is important.
The standard machine itself is two
metres long but offers the capability to
increase in length by bolting two sections
together to extend the bed when required,
converting the machine easily and cheaply
to a three/four metre model.
AddisonMckee
– UK
Email:
paspinall@addisonmckee.comWebsite:
www.addisonmckee.comNew numerical control system for
hydraulic bending machines
TRE C Srl is a manufacturer of bending
machines for metal profiles. Planning and
production, completely developed in-house,
relates to a range of sixty models of
bending machine with various powers and
technological solutions, up to CNC models.
Rollers and equipment are also an integral
part of Tre C’s production.
The company believes that the target of
improving the performance of machinery
and flexibility of application in various fields
should not prejudice the simplicity of use.
In response to these needs and thanks to
customer feedback, Tre C developed the
new numerical control CNW333, applicable
to all of its hydraulic bending machines.
The CNW333, developed on the
Windows XP operating system, can operate
in single- and multi-run, and is applied to
hydraulic machines both with two-speed
rotation motor as standard and with speed
regulator, which allows operation of four
processing axes with automatic speed
calculation.
In addition to the functions already
present in the other versions, it provides
a user-friendly programming system,
programming of up to 36 radii and automatic
positioning calculation for new bending
radii, facilitating processing performance
and programming. Files can be managed
directly in DXF format in order to obtain the
geometry to be performed and to create
network connections for interfacing with
other PCs for data exchange.
Tre C Srl
– Italy
Fax: +39 0558 877919
Email:
info@trecsrl.comWebsite:
www.trecsrl.comTre C’s CNW333 numerical control system, alongside
one of the company’s bending machines