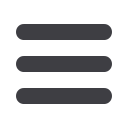

90
N
ovember
2011
www.read-tpt.com›
S
oftware
Software systems for
production and control
IN today’s market, where
margins for error are very
low, businesses need
not only a successful
strategy but also highly
efficient production and
logistic processes, with
controlled costs for each
article and stage of the
process. It is vital to
measure all operating
processes in real time
and with reliable data
in order to identify and
measure all the hidden costs, which require
timely corrective and preventive actions if
they are to be minimised.
We are clearly not referring here to
evident costs, which have obviously been
eliminated; we refer to the numerous little
wastages that we do not eliminate simply
because we are unaware of their existence.
Recovering efficiency can no longer involve
a single major point of improvement,
because if we had already done this long
ago we would not be in the marketplace
now.
STAIN has made and installed MES
solutions for steel mills, pipe manufacturing,
plastic moulding and drawing, die-casting,
taps and fittings and machining for over
20 years. The company’s experience has
taught it that gaining in overall efficiency is
the sum of numerous small improvements
throughout the production process. It is
therefore fundamental to measure all the
production and logistic processes at the
factory in real time to discover hidden costs,
which cannot be eliminated until they have
been identified and measured accurately.
Here is an example. We often fail to take
into account that the incidence of micro-
stoppages is a major factor in achieving
a significant improvement in efficiency. If
a machine stops for more than a hour,
everyone knows about it, but if the cycle
time is altered by a mere 3 seconds in a
minute to meet process requirements and
someone forgets to reset the standard time,
you risk discovering it much later when you
read the written report the following day,
and the loss is 5% on the total number of
items produced during the shift.
To eliminate these hidden costs in
production and logistics STAIN has
developed the STAIN+ suite based
on Siemens PLC technology, which
automatically gathers machine data and
integrates it with ERP, with automated
production and logistic flows via a fully
modular user-friendly solution. STAIN+
is a set of tools that provide a lens for
discovering hidden costs in the various
departments, and collecting machine
information automatically and in real time,
and a gauge for measuring the benefits
achieved by corrective actions implemented
in view of continuous process improvement.
STAIN+ is a comprehensive, modular
suite integrated with packages that include
data collection and production progress
monitoring, automatic identification of each
bin using barcode or RFID technology,
computerisation of logistic flows in the
departments, allowing the real-time
management of stocks and work traceability,
tool management (spindles, implements,
inserts, dies and moulds), quality and
statistical process control (SPC), and
preventive and corrective maintenance.
STAIN’s MES solutions – installed in
numerous important companies and
integrated with standard ERP – have
enabled many clients to use data collected
automatically from the field and convert it
into an invaluable and strategic asset for
the company, increasing their productivity
and marginality to double figures, often
well beyond their expectations. The main
organisational and economic advantages
are:
• automatic recording of times and
numbers of OK parts and rejects, with
accurate costing at each stage
• in-line inventorying, with stock reduction
and the elimination of physical inventory
times and costs
• reutilisation for other tasks of human
resources previously used for manual
production processes
• total elimination of transcription errors
and omissions as field production reports
no longer need to be compiled by hand
• real-time updating of work progress and
stocks, giving optimised scheduling and
reduced delays in delivery
• complete traceability of each container,
right back to casting of the raw material
in the event of non-conformities
• recovery of financial resources to
minimise stocks of unfinished products
(WIP)
• minimisation of tooling times and
computerised tool management (moulds,
matrices, inserts, plugs, spindles and so
on)
• increased awareness of global company
indicators by heads of department
• shorter stoppages thanks to an accurate
identification of causes
• accurate and prompt recording of rejects
by cause and field checks to enhance
product quality
• computerised inline checks at piloted
frequencies per article/machine to pre-
vent rejects and out-of-process errors.
If designed and implemented as a support
for organisational and cultural change
in the way of running a business, MES
systems can become a powerful means
for recovering margins as they discover
hidden costs, which are difficult to identify
without real-time integrated information and
become a strategic tool for the continuous
improvement of processes and our way
of operating. There are, however, two
fundamental requirements before this can
take place. First, both management and
organisation must believe firmly that having
integrated field and operating information
that is exact and functional to the company’s
organisational model is a real competitive
advantage and a strategic objective to
pursue with the necessary human and
technological resources. Second, the choice
of a competent and reliable partner with
specific skills in the sector that can provide
its experience in organisation, technological
development and, more importantly,
methodology in applying new technology in
the production bays.
Thanks to its lengthy experience in the
business and proven method of project
development and management, STAIN
can help businesses improve the efficiency
of their production and logistic processes,
via tailored advice and a comprehensive
standard suite with add-on modules, all
at a competitive price and extremely easy
to use.
STAIN
– Italy
Website:
www.stain.it