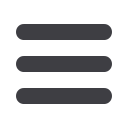

92
N
ovember
2011
www.read-tpt.com›
A
rticle
Acoustic microscope
finds “invisible” leaks
by Tom Adams, consultant, Sonoscan, Inc.
Tested under pressure, a bronze alloy pipe that was part of a pump
assembly appeared to be leaking at numerous locations, but close
visual inspection found no cracks. An acoustic microscope revealed
not only the cracks but also their unusual arrangement.
The sample of pipe described here measured 2.5 inches long, 1.25
inch in OD and 1.00 in in ID. Since it was designed to carry potable
water, the bronze alloy from which it was fabricated had been
modified to remove lead (Pb) and replace it with non-toxic bismuth
(Bi), a requirement of both state and federal regulators in the US.
This sample was one of a small number in one of the earliest
bismuth alloy lots to exhibit an unusual leakage pattern.
As part of routine testing, the pipe was filled with water under
pressure and observed for leaks. Water soon appeared on the outer
surface of the pipe, but it could not be traced to a single leakage
point. Instead, it appeared that water was leaking through the wall
of the pipe at numerous locations, and the pipe appeared to be
sweating. Pipes that leak during testing typically leak along a single
definable crack.
The next step was to stop pressure testing and examine the outer
surface of the pipe for leakage points. None were found, even
at very high optical magnification, although it is possible that the
texture of the machined surface might help to conceal very fine
cracks. The presumed cracks didn’t seem to be good subjects
for X-ray, so C-SAM
®
acoustic micro imaging was used because
of its reputation for being able to identify and image exceedingly
thin internal gaps, cracks, delaminations and the like. For acoustic
imaging, the sample was sent to Sonoscan’s
(www.sonoscan.com)headquarters laboratory in Elk Grove Village, Illinois, USA.
A C-SAM system uses a highly focused ultrasonic transducer that
raster-scans the surface of the sample at speeds up to 40 inches
per second. Each second, it sends thousands of pulses of very
high frequency ultrasound into the sample, and receives the return
echoes a few millionths of a second later.
The ultrasonic echoes come only
from material interfaces. If the sample
is homogeneous (as the wall of the
pipe sample should be), there will be
no echoes from the interior. If the
sample contains two or more bonded
materials, echoes will be sent back
from the material interfaces, such as a
metal to ceramic interface. The highest
amplitude echoes are reflected from an
interface between a solid and a non-
solid; the non-solid is nearly always
the air inside a gap of some type. A
homogeneous solid material such as
the pipe sample would be expected
to have no internally visible features
except cracks which, if present, will appear bright white (indicating
the highest possible amplitude) in the acoustic image.
Suppose that a metal to ceramic interface has over part of its area
a crack (or disbond, or delamination) that is 1mm thick. More than
99.99% of the ultrasonic pulse will be reflected when it strikes the
solid-to-air interface. If the crack is less than 1µ thick, it will still
reflect the same 99.99%+ of the pulse. What matters is the interface
between the solid material (metal, in this case) and the air in the
crack. The thickness of the crack doesn’t matter because essentially
no ultrasound crosses the crack to be reflected from the interface at
the bottom of the crack.
Most samples for acoustic imaging have at least one flat surface,
and the internal features, whether good bonds or gaps, are also
often flat. The transducer scans in a single x-y plane and creates
images of planar defects.
This sample, however, was cylindrical. Cylindrical samples are not
unusual, and Sonoscan has developed a fixture that permits the
transducer to scan along a single longitudinal line, pulsing and
receiving return echoes, and then pausing at the end of the line.
During the pause, the sample is rotated a fraction of a degree. The
transducer then scans back along the length of the sample, which is
then rotated again. Although reasonably fast, rotational imaging is
too slow for production environments and is best suited to laboratory
analysis. The transducer typically scans slightly more than the entire
circumference of the cylindrical sample – 365°, for example – to
give evidence in the acoustic image that the entire sample has been
examined.
The acoustic image of a small portion of the sample surface and
several cracks is shown in Figure 1. The sample was imaged using
an ultrasonic transducer with a frequency of 50MHz, selected to
give sufficient penetration and good spatial resolution.The ultrasonic
echoes that were used to make this image were “gated” on a very
shallow depth immediately below the sample surface. This means
that echoes only from this narrowly defined depth were used to
Figure 2
:
Deeper acoustic image shows the cracks within
the pipe wall
Figure 1
:
Acoustic image, focused and gated just below
the pipe surface, reveals cracks that are invisible optically