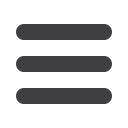

Industry News
www.read-tpt.com36
N
ovember
2012
Varnishing line commissioned
for the Salzgitter group
THE main target of the Provea project
was tube protection against corrosion
(most of the tubes are shipped,
increasing corrosion risks for the final
customer). The old machine used by
Salzgitter did not guarantee a good
result (tubes used to stick together
because of the thick layer of varnish).
The outside diameter range started from
20 up to 90mm.
The system designed is fully
automatic, from the initial bunch of tube
up to the storage table. A conveyor
drives the tubes throughout one closed
cabinet. The varnishing technology
chosen consists of two spray booths,
one on each side of the tube. Two
specific air guns have been placed on
each side of the tube. Varnish projections
that do not touch the tube are aspirated
by two powerful spray booth systems
(equipped with multilayer filters). All
electrical panels had to respect ATEX
standards, given the type of chemical
varnish used.
One of the key technical points was
the varnish thickness: it had to be
specially controlled. On the one hand,
tubes need a certain amount of varnish
in order to get enough protection
(around 20 microns). On the other hand,
the varnish has to dry before packing
and the level of varnish consumed has
to stay as low as possible. The testing
sessions enabled the company to find
the settings for the best result. The
different settings available on the new
line are: the speed of tube (up to 90
metre/minute), the air guns position
(relative to the tube), the varnishing
spray form, the flow level and so on.
The productivity initially aimed for has
been achieved. The quality of tubes
has dramatically increased (varnish
thickness controlled), opening new
markets to the Salzgitter plant. Provea
also works on complementary technical
systems for the line: pre-heating
solutions for tubes and drying systems
after varnishing.
Provea
– France
Email:
contact@provea-machine-tube.comWebsite:
www.provea-machine-tube.comVarnishing line