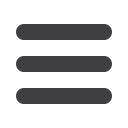

44
N
ovember
2012
Hire wire welding
of boiler tubing
FOR boiler manufacturing in the energy
industry, increased efficiency and
lower emission levels are increasingly
important. Overall life cycle costs have
to be reduced, which is only possible
by the use of advanced materials such
as P92 and T92, which guarantee high
temperature strength with reasonable
resistance to oxidation. This concerns
every new plant, as well as the
modernisation of existing plants.
For boiler tubing, only mechanised
TIG hot wire welding can be considered
for these newmaterials as a compromise
between quality and productivity.
During the prefabrication process
of boiler tubing for power plants an
important number of welds have to be
carried out in the workshop. Special
attention should be paid to the features
of the weld lathe at the beginning of the
assembly line. Here, different concepts
and types are presented and discussed.
During energy production in fossil fuel-
fired power plants, various types of fuel
areburned insidea combustion chamber.
The released heat is conducted to the
tube bundle inside the
surrounding boiler shell;
steam produced inside
the tube bundle is used
to power steam turbine
generators for electricity
production.
The boiler erection
operations can be divided
into three main parts:
making available the appropriate pipes
with matching dimensions, made of the
requested material, corresponding to
the specified quality level, shipped at
the desired date; prefabrication work
such as cutting, joining and bending
of the pipes in the workshop; and final
boiler assembly with the prefabricated
parts on site.
Pipes available on the market are
generally of fixed lengths, which depend
on production methods and transport
limitations.
During prefabrication, the pipes are
welded together to get appropriate
lengths for the pre-assembled units.
These are shipped to the site where
they are used to construct the
boiler.
The prefabrication can be
organised in two different
ways, which results in different
structures concerning the
production line and the
required equipment.
The first prefabrication
technique consists of welding
several
pipes
together
(depending on the length of the
delivered pipes, for example
two or three sections); the final
shape of the pre-assembled
unit is arrived at by joining
them with bends.
This prefabrication tech-
nique requires a welding
machine for the joining of the
tubes at the beginning of the
production line. At this stage
of operation the workpieces
are still rotationally sym-
metrical, so the welds are
carried out usually on rotating
tubes with the torch at a fixed
position. On the commonly
implemented welding lathe
the tubes are clamped,
centred and rotated at the desired
travel speed to carry out the weld. The
proper welding operation is performed
by means of the welding torch, which
remains in a fixed position.
The welded tubes are taken out of the
welding lathe and, after testing of the
welds and an in some cases necessary
heat treatment, they are assembled
using corresponding bends and form
pieces.
A significant number of welds have
to be realised, either manually, or
by means of orbital welding. The
production time of these pre-assembled
units can be considerably influenced by
the number of welding machines and
staff available to execute this work.
In
the
second
method
of
prefabrication, many pipes are welded
together. The final length corresponds
to the total length of the pre-assembled
unit, which can be up to 100m. Several
bending operations are then carried out
to transform the pre-assembled unit to
its final shape.
This type of prefabrication requires
virtually all welds to be carried out by
the welding lathe or tube welder at the
beginning of the assembly line. The total
production time of each pre-assembled
unit is influenced strongly by the capacity
of this machine.
Due to the importance of these straight
tube welders their design has been
continuously improved and adapted to
the specific needs of production. With
the increase in efficiency of power
plants, higher service temperatures
became necessary and new heat-
resistant materials had to be developed,
making welding operations more and
more delicate.
Polysoude SAS
– France
Email:
info@polysoude.comWebsite:
www.polysoude.comTechnology News
Use of “straight tube welder”
in boiler manufacturing