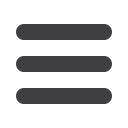

Tube and pipe mi l ls
www.read-tpt.com88
N
ovember
2012
OMP s.r.l.
- Italia, via Delle Prese 42/44 Z.I. - 36014 Santorso (VICENZA) ITALY tel +39 0445 640822 fax +39 0445 640225
info@omp-group.itOMP worldwide presence :
Argentine - Austria - Belgium - Bulgaria - Brasil - Canada - Cyprus - Denmark - Estonia - Great Britain - Jordan - Estonia - Finland - Germany - Greece - Holland - India -
Iran - Italy - Israel - Korea - Malaysia - Mexico - Norway - Polonia - Portugal - Czech Republic - Russia - Slovenia - South Africa - Spain - Sweden - Turkey - Ukraine - U.S.A.
OMP Taglio Tecnologia
- Brasil, R. XV de Outubro, 1754 CEP 89239-700 Rio Bonito - Joinville - SC Fone +47 3473 7200
contato@omp-taglio.com.brLATEST TECHNOLOGYAROUND TUBE
CUT TYPES
Automatic cutting machine for structural tubes, hydraulic working with double pump
system and head feeding controlled by a proportional valve system. 3 controlled axis,
can do angle cut at +60°/-75°. Suitable for big diameter and thickness, connectable
to different types of loading and unloading systems.
Automatic bundling line for round, square and rectangular tubes
or solid bars. Can package in square, rectangular and hexagonal
bundles. High productivity systems can be customized on
customers’ specifications.
TUBE BUNDLING LINES
KR3
- Cutting lines from ø12 to ø200
- Deburring machines
- Chamfering machines
- Multiheads cutting machines
- Tube bundling machines
OMP HRP MACHINES SALES PVT LTD
- India - Palm Spring Building Unit 616, Above Croma, Link Road Malad (W) Mumbau 400064 -
www.hrpsales.com www.omp-group.itAdvances in equipment design:
universal forming and cassette stands
KUSAKABE Electric & Machinery Co Ltd
of Japan, a leading pipe and tube mill
manufacturer, is continually developing,
innovating and improving the design and
manufacture of pipe and tube mills for the
international market. From API, oil, gas
and structural to automotive and general
engineering applications, Kusakabe can
supply the whole mill or individual pieces
of equipment to meet your production
requirements. All of the equipment is
designed and built in Japan to exacting
Japanese standards and workmanship.
The forming section of the OG&S
mills is made up of an entry guide, the
universal forming section followed by
the patented cassette style fin pass
section. The universal forming section
includes the breakdown passes and all
the forming up to the fin pass stands.
Size changes are fully automatic
and controlled by the motorised roll
positioning equipment in conjunction
with an HMI (human machine interface)
screen with its menus and recipes. The
positioning of the rolls is driven to the
predetermined optimum position for
each product.
The forming section using universal
tooling requires no rolls to be changed;
the position of the rolls are adjusted to
suit all the diameters to be made. The
Kusakabe universal forming is designed
so that the strip is easily visible as it
progresses through the forming process.
This makes it easy for operators and
engineers to see what is happening in
the forming process. The forming flower
used to shape the pipe minimises the
work hardening while providing for the
ideal edge presentation for HF welding.
The fin passes are cassette stands
and typically consist of three-, four-
roll stands where two of the rolls are
driven in each stand. This design
allows for a very strong stand plus the
added strength of the cassette results
in considerably lower distortion under
load than the conventional stand
configuration. The position of the four
rolls can be individually adjusted and
the position of the cassette can also
be adjusted, which allows for easy
adjustment of the pass line height. As
the four rolls are contained within a
cassette, when it comes time for a size
change all of the cassettes are changed
at the same time.
The cassette changeover is conducted
automatically and typically takes 10 to 15
minutes with no operator involvement.
When the changeover is complete the
motorised roll positioning equipment, in
conjunction with the HMI screen and the
menus and recipes, positions the rolls at
the predetermined optimum position for
each product.
Kusakabe Electric & Machinery Co
Ltd
– Japan
Email:
sales@kusakabe.comWebsite:
www.kusakabe.com