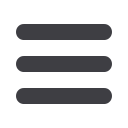

Institute of Measurement and Control Functional Safety Conference 2016
Challenges in Achieving Safety Instrumented Function Response Time for a Fast-Acting Process
Page 4
causes may result in a single hazardous event, resulting in difficulty in estimating the PST (Summers,
2008). It is therefore necessary to establish the single worst case variable, which initiates the hazardous
event, from which the PST can be estimated.
The amount of rigor required in determining the PST will depend on the integrity required within the
system. More critical and time dependent systems will require a higher degree of assurance and the most
rigorous approach. Estimation of the PST can be performed using qualitative analysis, a simplified
quantitative analysis or a dynamic quantitative analysis.
A qualitative analysis may be used for cases in which determination of the PST is not practical. This
approach utilises engineering judgement based on past operational experience, manufacturing guarantee
or other engineering justification to qualify the PST. A simplified quantitative analysis is one where the
scenario can be simplified such that a simple correlation and a spreadsheet can be used to estimate the
PST. Such an example is in the case of using level control to initiate a SIF response where the PST can be
determined based on known design and operating parameters.
A quantitative dynamic approach is used when both a qualitative method and a simplified quantitative
method cannot be used. This method involves the use of proprietary software to simulate the transient
hazardous scenario and observe the behaviour of the process after triggering the cause of the system
upset. This method is considered the most realistic approach, but is the most complex. Validation of all
input data, regardless of the approach, is important to provide accurate results.
Measured results from recorded incidents and plant operating data increase the likelihood of accurately
estimating the PST and it is recommended that this information is used where available. Accurate
information about the dynamic nature of the process is required to properly develop the process
simulation. This can be obtained from measured plant data (Varga and Abonyi, 2010).
For the example, the use of a temperature trip was recommended to isolate the upstream piping system
and protect the downstream piping from the temperature escalation. The following information was
required to determine the PST:
1)
Basic process operating information (design/measured operating parameters).
2)
Equipment design limitations (piping low temperature limit) to determine the safe design limit of
the system.
3)
Piping isometrics and equipment specifications and design data.
There were several causes for the low temperature excursion in the system analysed. One of the scenarios
which resulted in the low temperature scenario was overflow of an upstream vessel resulting in flooding
of the downstream heat exchanger and a higher heat transfer to the downstream system. Determining the
PST using the vessel liquid level as the measured variable results in a larger PST as the sequence of
events to the hazardous event is longer. This PST would include the time required to overfill the vessel,
the time for the cryogenic fluid to reach temperatures beneath the low temperature limit of downstream
systems, and the additional time for this fluid to reach the emergency shutdown valves before the system
was shut in. Therefore, the use of temperature as the measured variable to calculate the PST was deemed
more conservative than using level.
Observed data was available for the maximum rate of change of temperature over time during an upset,
and this served as input into a dynamic process model. The model was built using piping and equipment
dimensions to model the available fluid volume. The model was then used to simulate the upset condition