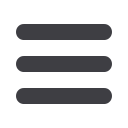

Institute of Measurement and Control Functional Safety Conference 2016
Challenges in Achieving Safety Instrumented Function Response Time for a Fast-Acting Process
Page 7
in the input (Liptak, 2006). Typically, the response times of pressure sensors are much faster and more
predictable than those for temperature sensors.
For the example, the following technologies were considered for the sensing elements – temperature
using resistance temperature detector (RTD) and thermocouple; and level using differential pressure and
guided wave radar (GWR). Temperature sensors were found to have the slower response times owing to
the response time of the thermowell and, in the case of skin temperature devices, the pipe wall. Generally,
grounded thermocouples have a faster response time than RTDs, although in our example, some
manufacturers were able to provide faster acting devices using RTD technology. Level measurement
using differential pressure technology had a fast response time, except for which capillary tubes with fill
fluid were required. Through air level measurement devices require digital processing to filter noisy
signals. This results in slow response times. Guided wave radar provides an almost instantaneous
response if no additional filtering is required. However, one supplier indicated that there was no published
data for response time of their guided wave radar devices.
Response Time
For the temperature element, various manufacturers proposed methods of increasing the response time of
the thermowell such as using non-standard shapes and textures, conductive paste and spring loaded
thermowells. The result of this was to decrease the air gap between the element and thermowell and
increase heat transfer between the element and the process. However, this still did not reduce the response
time to an acceptable value. For the differential pressure transmitter, the use of capillary tube with fill
fluid was considered because of the temperature of the process. This significantly increased the response
time of the device. In one instance, the manufacturer indicated that the response time could increase from
less than 1s without the capillary tube to 10s or more, depending on the length of tubing used.
The typical rule of thumb for estimating the response time for a valve is 1 inch movement per second. For
the example, this response time was not acceptable so a quicker responding valve was required. The
manufacturer was able to recommend a valve and actuator designed for faster response. To increase the
response time, a quick exhaust valve was mounted on the actuator. This has a larger output port than that
of the actuator and thus enables more air to be exhausted on activation of valve closure.
Kull (2015) recommends methods for estimating the response time of the logic solver. The safety system
response time includes the delays resulting from hardware (analog and discrete input/output modules) and
processing delays. The selection of method used is dependent on the demand mode (low / high /
continuous), configured delays on input elements, code organization, number of program cycles for code
execution, system faults and noise blanking, and maximum cycle time of the controller. To improve
response time of the controller, functions can be restructured and specific tasks can be prioritized over
others. For the example, owing to the age of the safety system and lack of clear definition within the code
organizations, a large design margin was used.
Non-Deterministic Elements
It was found that, although response times for devices which utilized mainly electronics were fast-acting
and deterministic, the response times of mechanical devices, such as the thermowell and capillary with fill
fluid, were higher and less deterministic.
Using the thermowell as an example, Liptak (2006) explains that to measure the response of the
temperature sensor, in-situ testing is required because the response time is a function of process