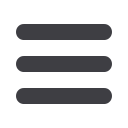

Institute of Measurement and Control Functional Safety Conference 2016
Challenges in Achieving Safety Instrumented Function Response Time for a Fast-Acting Process
Page 8
temperature, pressure and, most critically, flow rate. The effect of process pressure and flowrate is as a
result of the heat transfer of the surface; however, the effect of process temperature is also determined by
the thermowell’s internal composition and geometry. The response time due to changing process
temperature is, therefore, more difficult to predict as it is affected by expansion and contraction of air
gaps within the material which can alter the shape and material properties of the sensor.
In the cases for which response times were quoted for sensor/thermowell combinations, these were done
under specific test conditions. For example, a response time would be quoted under at a particular
flowrate in a particular medium. Although estimates could be provided, there was no written guarantee
that under the actual process conditions, the sensor would have similar performance.
One operator developed calculation based on the article “Optimal Selection of Thermowells” ISA
Transactions Volume 34, Issue 2, June 1995, was used to predict the response time of thermowells
proposed by manufacturers. (ISA Transactions, 1995) However, the results of these calculations did not
correspond to those predicted by manufacturers for which special thermowells and conductive paste were
used.
When using the capillary tubes, the manufacturer indicated that the response time is influenced by a
number of factors such as the type of fill fluid, the length of tube and the quantity and orientation of bends
in the tubing. Estimates of time delay per length of tubing could be provided. However, the manufacturer
indicated that the best method of determining the response time would be during a functional test. This
would take place only after the design is completed and the device is purchased.
The response time for the actuator using the quick exhaust valve was provided. However, a rule of thumb
of an additional 25% was used for the response time of the valve itself. Again, this was only verified after
a bench test.
Other design factors
Alternatives were considered such as the use of the temperature sensor without a thermowell. However,
because the application was a flowing stream, this would present an additional hazard resulting from
induced vibrations in the element. In addition to this, by use of non-standard thermowells, the response
time may be achievable but typical wake frequency calculations could not be done in accordance with
ASME PTC 19.3 TW for Thermowells because of non-standard geometry. Vibration checks would
require computational flow dynamics or finite element analysis and would require significantly more
effort.
Accuracy and Calibration
For fast-acting processes, the accuracy of the instrument is a critical factor in achieving the SIFRT. This
contributes to the estimation of the design margin between the SIFRT and PST. If the accuracy is low,
then there should be a greater design margin. Thus, although the design margin should be established
early in the design phase, this may be an iterative process while the design progresses, to account for
uncertainties in the design.
Furthermore, the calibration of the instrument is important because the device can have an offset in
measurements.