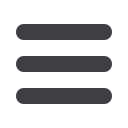

EuroWire – May 2011
40
technology news
The PDH lubrication system is used
in the most demanding drawing
applications, allowing highest drawing
speeds, with all carbon steel rods/wires,
mechanically descaled or acid cleaned,
bare or pre-coated, including spring wire,
high-tensile rope wire, plating wire, cold
heading wire, etc.
The system is highly regarded for its
unique ability to convert a solid lubricant
into a liquefied solution and maintain its
thermal stability (at 200 to 240°C) at all
drawing speeds.
The
PDH
system
achieves
a
high-performance wire rod dry coating/
lubrication
with
completely
fused
lubricant deposited instantaneously on
rod/wire surface, operating at zero energy
consumption, performing a high-density
strongly adherent anti-wear multi-layer
coat with adjustable weight, completely
eliminating the need for phosphate and
borax wet pre-coating chemicals.
The PDH lubrication system prevents
metal-to-metal
contact
at
wire-die
interface, enabling frictionless drawing,
providing superior surface quality and
improved wire ductility.
Decalub – France
Fax
: +33 1 60 20 20 21
:
info@decalub.comWebsite
:
www.decalub.comADVERTORIAL ON BEHALF OF DECALUB
The DCCD (Dry Cleaning, Coating and
Drawing) process offers substantial cost
savings in the most demanding drawing
applications from mechanically descaled
bare rod, drawn directly without wet
pre-coating chemicals, including spring
wire, PC strand wire, cold heading wire,
plating wire, etc.
The process operates at ‘zero’ maintenance
cost as there is no acid, no hot liquid tanks
for rod pre-coating, no hot air blowers to
dry wet rod, and it operates at virtually
zero energy consumption.
An added benefit is the automatic control
of lubrication parameters, including
lubricant pressure, temperature and
viscosity, enabling the use of standard high
melting lubricants (+220°C/428°F) which
are converted from solid into liquefied
state and deposited on bare rod in a few
microseconds, generating exceptional
thermal stability at the highest drawing
speed, eliminating phosphate, borax and
their wet substitutes.
In operation, all these parameters
‘communicate’ together in a sensitive
and automatic multi-way interaction
to form a hard and strongly adherent
full-film
anti-wear
lubricant
coat,
weight-adjustable, enabling frictionless
drawing
by
physical
separation
of wire-die contact in all drafts,
eliminating friction heat.
Typical applications of the DCCD
process are: output of 2.2 tonne/
hour with 5.5mm 0.83/0.88%C rod,
in a ‘frictionless’ drawing application
with die life of 200 tonnes/die in the
first draft and a die wear of 0.1 to 0.3
micron/tonne of wire drawn in the last
draft.
Spring wire is drawn from mechanically
descaled bare rod, without pre-coating
chemicals, at 18m/s (3,600ft/min);
5.5mm 0.72%C rod drawn to 2.35mm
at
16m/s
(3,200ft/min);
10.5mm
0.85/0.88%C rod drawn to 4.22mm at
9m/s (1,800ft/min).
Decalub – France
Fax
: +33 1 60 20 20 21
:
info@decalub.comWebsite
:
www.decalub.comDecalub’s pressure-die
anti-wear lubrication
Rod dry preparation
and direct drawing
▲
▲
Rod cleaning and wire drawing by DCCD process
IN
THIS
ISSUE
No data
loss from
cables