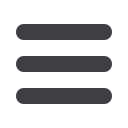

EuroWire – May 2011
52
Drawing dies & cones
High pressure die from Redies
The lubrication is one of the crucial
factors for the quality of the drawn wire.
An interrupted lubrication in the
steel wire drawing process causes an
increase of surface tension in the wire,
strong pressures inside the die, rapid
die wear, breakage of the drawing
nib and consequent non-programmed
interruptions in the wire drawing
process.
In order to avoid these problems, Koner
has studied a new concept line of
drawing dies – K. 340 and K.370 pressure
drawing die (patented worldwide),
specially constructed and designed
to greatly improve lubrication in dry
drawing of steel wire.
For the drawing the K.320 tool has been
created, which allows wet drawing
process characteristics and also a great
economic saving.
The K.340/K.370/K.320 methods provide
considerable operating advantages:
• Production at maximum drawing
speeds
• Less machine down-time for die
replacement
• Better and more homogeneous wire
quality
• Wire drawing under optimum quality
control
• Nib life increased by 30% and more
to traditional dies
• Overall costs reduced by around 40%
(you only change the nib and not the
entire die)
• Application
of
the
requested
quantity of lubricant coating to the
wire
• Better wet or dry redrawing
operations
• The overall dimensions of K.340/
K.370/K.320 tools are the same as for
traditional dies
• Savings on transport – even large
quantities of nibs can be delivered
rapidly in small packages directly to
customers in any part of the world
• Elimination of die rejects and the
accumulation of no longer useable
drawing dies in the warehouse.
A return can also be gained from the sale
of worn tungsten carbide parts.
Koner – Italy
Fax
: +39 025 455 832
:
tkt@tktgroup.itWebsite
:
www.tktgroup.itCarbide dies and steel tools
Hedalloy is a tool and die machine shop formed in 1947. The company’s equipment
includes manual and CNC lathes, hones, mills, surface grinders, ID grinders, OD
grinders, machining centres, sinker EDM, wire EDMS and hydraulic press.
The company manufactures all
tooling necessary for nut and bolt
makers, hot and cold headers,
presses,
hammers,
upsetting,
extruding, forging, metal forming,
wire draw equipment and others.
It
can
design,
engineer
and
manufacture
part
development
packages on multi-station machines
to efficiently produce special cold
formed parts from coiled wire.
Hedalloy
manufactures
quality
carbide and steel tooling such as
carbide die and punch assemblies
– new and rework or repair, casings,
holders, sleeves, inserts, wafers, plates, strippers, shedders, die kick-out pins and
punches (piercing, extruding, stamping, round, square, hex, torx, lobed, slotted, phillips,
spline, raised lettering, characters, engraved, 12-point, socket and customised/special).
Hedalloy Die Corp – USA
Fax
: +1 216 341 5393
:
hedalloy@sbcglobal.netRedies – the central European die maker – has developed a High Pressure Die (HPD)
combined from TC and polycrystalline diamond inserts.
The die consists of three interchangeable/renewable parts screwed and tightened
into a mounting with standard outer size 43 x 30mm. The drawing part is made from
MANT® PCD.
The HPD has proved to give a better surface and a longer lifetime with drawing wet as
well as dry the following materials: stainless steel, high carbon steel and spring wire.
Redies Srl – Italy
Fax
: +39 0362 852 078
:
info@redies.comWebsite
:
www.redies.com▲
▲
Carbide assembled quills for wire
▲
▲
The Redies TC-PCD high pressure die
Crucial factor
for quality of
drawn wire