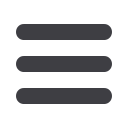

20
MODERN MINING
December 2016
GEOTECHNICAL
ENGINEERING
T
here had been a number of rockfall
incidents reported over the years
emanating from the western slope
of the SJ pit with debris landing on
the Trolley 14 access ramp. This
ramp is one of the major arteries of the SJ pit
and was designated as the main access for the
life of mine.
The slope above Trolley 14 was designed
to be 15 m high benches with a 10 m catch
bench; in most cases, however, the crest was
over-mined due to extensive blast damage
caused within the sub-drill area. The resultant
rock mass comprised a loose package of jointed
blocks hanging along the crest of each bench
face, which provided a source for rockfall.
Temporary measures to mitigate the rockfall
risk had been put in place by the mine but a
long-term solution to the problemwas required.
Geobrugg visited the site with Fairbrother
Geotechnical Engineering and discussed the
client’s requirements. A drape mesh system
was considered the most suitable system as it
was the most cost effective and efficient, pro-
viding a long term solution to ensure that the
trolley line is protected from rockfall and mini-
mising the safety risks during installation.
The installation process was also a signifi-
cant factor owing to the surface area under
consideration, as well as the mine’s require-
ment to keep the trolley line open for as much
of the construction time as possible.
Drape mesh
system provides
rockfall
protection
at Rössing
Anchor system for the
drape mesh at the crest
of the slope.
Towards the end of 2015, Fairbrother Geotechnical Engi-
neering approached Geobrugg to help themwith a design
solution at Rio Tinto’s Rössing uraniummine near Swakop-
mund in Namibia. The request was to address the rockfall
hazards on the wall above the Trolley 14 access ramp, an
area of 110 m high by 270 m long. The solution adopted
was a drape mesh system.