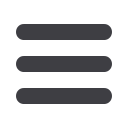

December 2016
MODERN MINING
21
GEOTECHNICAL
ENGINEERING
The installation of the drap-
ing systemwas managed
by Fairbrother Geotechni-
cal Engineering using
their own employees and
supplemented by seven rope
access technicians (RATs)
provided by Alpinist Safety
Consultants (ASC).
For that reason industrial rope access tech-
niques were proposed to the mine with the
additional sub-contract appointment of a spe-
cialist company, Alpinist Safety Consultants
(ASC), with a track record of successfully and
safely executing difficult drape system installa-
tions in the civil engineering market.
The Geobrugg Rockfall Drape design soft-
ware was used to determine the most suitable
and economical solution which resulted in a
number of draping options being discussed
and a solution negotiated with the client to fit
the budget allocated for this slope. The final
solution was a combination of 16 500 m
2
of
QUAROX
®
rolled cable nets (3,9 m x 30 m per
roll) overlayed by DELTAX
®
mesh (secondary).
The superior qualities of QUAROX rolled
cable nets compared to conventional cable
nets allowed for easier and more efficient
installation. No extra work was required
before unrolling down the slope which pro-
vided for a 30 % reduction in installation
time. The QUAROX fits unobtrusively on
the slopes and can be colored using powder
coating to give it an even better visual appeal.
The chain link construction of the cable nets
offers much better force transmission than
traditional connection by cross clip. Standard
support ropes, seaming ropes and shackles
are used for the installation.
This project was a first as the QUAROX Plus
drape system had not previously been used in
an application in the mining sector in Africa.
The installation of the draping system
was managed by Fairbrother Geotechnical
Engineering using their own employees and
supplemented by seven rope access technicians
(RATs) provided by ASC. The proximity of a
haul road at the top of the slope allowed for
the provision of track-mounted crawler rigs to
install the anchor system for the drape mesh
at the crest of the slope. This haul road further
enabled Fairbrother to provide a more efficient
service to the technicians by using a crane to
lower the mesh panels into place before send-
ing the RATs down the slope to fasten the
panels into place.
Additionally, to assist the mine with its
desired use of the trolley line, a 2 m high berm
was constructed in the middle of the road as an
exclusion barrier allowing for the trucks to con-
tinue hauling payload up the trolley line whilst
the RATs installed the drape mesh.
Safety was of paramount importance to all
the parties and was a non-negotiable on this
project. The fast installation methods required
that three self-contained teams of RATs work
on the slope at the same time clipping the mesh
panels together and it was vitally important
that there was never a ‘crossover’ between the