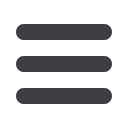

CAPITAL EQUIPMENT NEWS
JULY 2017
18
addition of a refurbishment programme
to its breadth of services and equipment
for the mining and aggregate industries.
The new programme gives customers the
opportunity to save as much as 40% over
buying new, while having the assurance
that their refurbished machines will
operate at peak capacity.
“As an industry leader, we offer our
customers an array of services and
upgrades to improve their equipment and
add value to their process, which is why
we added refurbishment to our circle
of offerings,” says Karen Thompson,
president of Haver & Boecker.
Peter Kilmurray, vice president of Sales
at Haver & Boecker, says the company
has the capacity to update old screening
equipment with all the bells and whistles
of new technology, at nearly half the cost
of purchasing a new machine.
As part of the programme, Haver
& Boecker’s technicians inspect and
document all critical components and parts
on a vibrating screen onsite or at the new
Haver Service Centre. Each customer then
receives a complete report documenting the
specialists’ recommendations. Technicians
improve screening performance by
implementing necessary upgrades using
both new and re-engineered components.
Refurbishments can take as little as
one week to complete, depending on the
scope of the work. They include everything
from installing wear liners to replacing the
shaft or adding an automatic lubrication
system to extend bearing life. Following
the refurbishment, Haver & Boecker tests
the vibrating screens with Tyler’s Pulse
vibration analysis service programme,
which monitors the health of vibrating
screens to ensure optimum screening
performance and equipment durability.
Once completed, the machine is painted
and leaves the Haver Service Centre
looking brand new. All refurbishments
include a one-year warranty. For more
extensive coverage, customers may opt
into an asset management programme
tailored to each operation that includes
monthly, quarterly or yearly equipment
audits by certified technicians, whose goal
is to increase equipment lifespan.
Engine rebuilds
With commodity prices at historic lows in
recent years, it has become popular for
mining companies to overhaul essential
equipment components. According to
Cummins Southern Africa, a prominent
engine manufacturer, there has been a
significant increase in demand for critical
rebuilds of high-horsepower engines as
mining companies seek to optimise the
lifecycles of their equipment.
To meet the increasing demand, the
engine maker embarked on a R5,4 million
capital expansion programme in late 2015
to accommodate bigger engines such as
the QSK78, which weighs in at 10,2 t,
at its Master Rebuild Centre in Kelvin,
Johannesburg, South Africa. It services
the whole of southern Africa, including
Botswana, Zambia, Mozambique, Namibia
and Zimbabwe, covering mining and other
high-horsepower applications.
Since 2010, the company has noted
increasing demand for rebuilding services
for its high-horsepower range from the
QSK 19 to QSK 78, according to Patrick
Mohale, leader at Cummins SA’s Master
Rebuild Centre.
Cummins Southern Africa’s high-
horsepower facility was established as
part of the engine maker’s international
strategy, announced in 2012, to increase
high-horsepower engine remanufacturing
capacity by 100% to meet demand for “a
rapidly expanding population of mining
equipment powered by its popular QSK
and K-Series engines”. At the time, the
engine maker said it would double total
high-horsepower rebuild capacity to about
7 000 units per year by 2016, compared
with the 2011 capacity of about 3 500.
Cummins’ engine rebuild process is said
to offer “as-new” reliability and life-to-
overhaul, and also carries a new warranty
of 12 months and unlimited hours. The
high-horsepower range spans from 450 hp
to 3 600 hp and encompasses engines with
displacements of 19, 23, 30, 38, 45, 50, 60
and 78 litres.
Increasing capacity
Mohale says the 3 366 m² Cummins Master
To meet the increasing demand for engine rebuilds, Cummins embarked on a capital expansion
programme to increase the capacity of its Master Rebuild Centre in Kelvin, Johannesburg, South
Africa.
When buying rebuilt gear, it is of utmost significance to ascertain that the refurbished piece of
equipment has a warranty and maintenance programme.