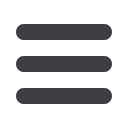

Rebuild Centre has the capacity to perform complete rebuilds, partial
rebuilds, warranty repairs as well as fix-as-fail services. “Fix-as-fail
is when the engine fails at the mine site and has to come back to us.
We troubleshoot to understand why it failed and we replace what is
damaged,” says Mohale.
The facility also has the ability to dyno test every engine after
rebuilding to ensure engines perform to specification. To cater for
this, Cummins Southern Africa invested in two dyno testing cells
(800 hp and 4 650 hp) as part of the 2015 upgrade.
When an engine arrives, it comes with an instruction of what
work should be done on it. The life history of the particular engine is
also supplied. This includes previous issues it had and what sort of
maintenance was carried out, as well as the whole service history.
The information is provided by Cummins service technicians based
at the mines, as well as area managers in different locations where
the engines are operating.
Once the instructions and the life history have been received, the
engine is dismantled in order to provide a quote. This is to ensure
that the cost of fixing it will not outstrip the cost of buying a new
one. In these circumstances, the customer is advised accordingly.
“It is important that once we dismantle the engine we put together
a quotation and only go ahead with the job when the customer
agrees,” says Mohale, who notes that there are some instances
during zero-hour rebuilds that they discover damaged engine blocks,
and this may in some instances lead to high rebuild costs. In these
circumstances, buying a new engine is a better option than trying
to fix it.
Most of the processes are done in-house, except for some
machining processes on the blocks, cam shafts, con-rods and
crankshafts that are outsourced to a service provider, Metric
Automotive Engineering.
b
Haver & Boecker has announced the addition of a refurbishment
programme to its breadth of services and equipment for the mining
and aggregate industries.