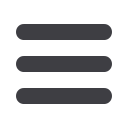

EuroWire – May 2012
57
F c s
Italy
THE Falcon Topscan AWM system allows
fully automatic thickness measurement
on insulating covers and non-metallic
sheathings of electric cables.
The system, developed by Falcon
Instruments, is a natural evolution of the
profile projector or of the measuring
microscope, and was designed to
provide measurement objectivity and
repeatability of results, along with time
and manpower savings. It conforms to
CEI 20-34/1-1 and the most important
international standards.
At the push of a button, the system
measures the thickness of inseparable
insulating covers and sheathings, giving
single thickness measurements. The
system is also able to work with varying
height cable samples and with a single
parallel plane. This is possible due to
a particular disposition of the camera,
which allows it to acquire the face of the
sheathing that is directly on the bearing
surface. The instrument features a double
interface level: the first level is for the line
operator, and the second for a supervisor
or for those who are in charge of quality
laboratories.
All of the systems in the product line
have been developed by the criterion of
the Falcon MMI interfacing with the user,
based on the concept of ‘press a button
and measure’.
The instruments have measurement
repeatability of 1/4,000 of the field of
view, and measurement reliability of
1/2,000. For example, the repeatability
of the instrument with a 20mm field of
view is equivalent to ±0.005mm, with
instrument reliability equivalent to
±0.01mm.
Emmerre Srl – Italy
Website
:
www.emmerresrl.comEldes produces and installs real time
control systems applied to metal cold
forming, both cold headers and thread
rolling machines. They are based on
the supervision of the force developed
in the production process, by means
of piezoelectric sensors applied to the
sensitive points of the structure. This type
of control is a necessary condition for
starting a production cycle even when
operators are absent.
The first control systems entirely based
on Italian technology were developed
by Eldes in 1982. Preserving continuity
and always looking for innovation,
Eldes followed, and often anticipated,
progress in cold forming technology,
developing the new generation of
process monitoring to which Helios 2K
and Titanus 2F belong.
The company’s aim was to give the
operator a means to understand and
oversee the forming process, tailoring
the controls according to increasing
needs and continuously improving the
man-machine interface.
The technological know-how developed
in cold forming allowed the company to
create dedicated networks for production
data
collection
and
dimensional
measurement
acquisition
systems.
The shop floor data collection network
enables complete control of data
production in the directional centre of
any manufacturing company specialised
in cold forming, without time consuming
manual intervention.
To control production quality, Eldes
software solutions guide and help the
operator in the job of measuring produced
parts, by directly providing all the
necessary data and by obtaining all the
documents the company system requires.
The station structure plays an important
role and is therefore part of the supply.
Eldes snc – Italy
Website
:
www.eldes.netThickness
measurement
Get in real time control
▲
Helios 2K monitor