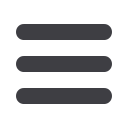

EuroWire – May 2012
63
F c s
Italy
SIRIO Wire Srl specialises in the
production of wire surface treatment
lines. Its production range includes HCl
fumeless pickling, H
2
SO
4
electrolytic
pickling, ultrasonic and electrolytic
cleaning, electro-plating lines, bronzing
lines for beadwire, phosphating, coating
and drying.
Demand for cleaning processes in
the wire industry is continuously
increasing, along with increased quality
requirements. Ultrasonic cleaning allows
the removal of products present on the
surface of the wire, such as calcium and
sodium stearate lubricant coming from
the dry drawing machine, lubricant
oil from the wet drawing machine,
phosphate coating and others.
The main applications can be found in the
field of stainless steel wires, oil tempered
wires prior to heat treatment, carbon steel
wires prior to galvanising, and aluminium
alloy wires.
Ultrasonic cleaning is the use of high
frequency sound waves. In the activity
called cavitation, micro-sized bubbles
form, grow and implode due to
alternating positive and negative pressure
waves. Just prior to each bubble’s
implosion, there is a tremendous amount
of energy stored inside the bubble itself.
The implosion event, if it occurs near
a hard surface, changes the bubble
into a jet, which travels at a speed of
approximately 400km/h towards the hard
surface. Because of the inherent small
size of the jet, ultrasonic cleaning has the
ability to reach into small crevices and
removed entrapped soils very effectively.
The basic components of an ultrasonic
cleaning
system
include
ultrasonic
transducers, an electrical generator and a
tank containing the cleaning solution. The
ultrasonic generator converts a standard
electrical frequency of 50 or 60Hz into
the high frequencies required. The higher
the frequency, the smaller the bubbles
created during the cavitation will be.
The transducers are constituted of PZT
elements (Pb-Zr-Ti) that convert the
electrical energy in mechanical vibrations
by piezoelectric action. The transducers
are installed inside a watertight box
made of stainless steel, immersed in
the cleaning bath and located some
centimetres below the wire field. A
watertight cable connects the transducer
holding box to the generator.
After the cleaning operation, it is
necessary to thoroughly rinse the wire in
order to remove the chemical residuals.
Sirio Wire has developed a special system
working with water under pressure to
allow the best rinsing effect. All Sirio
Wire equipment is fitted with special
mechanical drop traps and effective air
wiping devices to minimise the liquid
drag out.
SirioWire Srl – Italy
Website
:
www.siriowire.comSpecialising in wire
surface treatment
▲
Cleaning technology from Sirio
Cleaning and plating technology
Otomec Srl engineers and manufactures customised cleaning and plating plants
for the wire, cable and strips industry. The company can provide a wide range
of machines, sized to process small volumes of product as well as large outputs,
single-multi strand, reel-to-reel, and speeds up to 20m/sec.
OTO 5 is a modular, multi-functional plant for in-line preparation of iron wire rod,
patented and awarded by the European Community for innovative features, while
OTO 4 is a complete plant for the electroplating of steel and non-ferrous wire.
The OTO’FF line is a reel-to-reel or basket plant for copper, brass, stainless steel,
carbon steel, superconductor, alloys and fine tubes. The model OTO 2 performs in-line
coppering of up to 5mm wire, at speeds of up to 20m/sec. The company also produces
compact plants for environmental treatment (water, steam) and auxiliary plants.
Otomec operates worldwide, providing exclusive technology as a result of almost
one hundred years of experience in the field.
Otomec Srl – Italy
Website
:
www.otomec.it