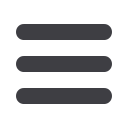

EuroWire – May 2012
67
Technical article
Similar tensile strengths are obtained in
the Base and B steel whereas the High B
steel exhibits an ultimate tensile strength
lower by about 50 MPa.
This lower strength value may again
be
related
to
increased
austenite
decomposition kinetics. Slightly higher
total elongation is obtained for both
boron containing steels.
The patented wires were subsequently
drawn to 1mm diameter in consecutive
passes and resultant tensile properties
in addition to number of twists to failure
(Nt) and number of reverse bends (Nb) are
given in
Table 4
.
A decrease in tensile strength with boron
alloying is again apparent along with
a slight increase in uniform and total
elongation. The number of twists to failure
is however not altered by the alloying
whereas a slight decrease in number of
reverse bends is observed with increased
boron levels.
In order to assess aging response of the
1mm drawn wire, isothermal aging was
conducted at 150ºC for one hour and the
results are given in
Table 5
.
A tensile strength increase by about
170MPa is obtained whereas tensile
elongations are reduced to 0.4% uniform
and 1.5% total elongation. Similar
elongations were obtained in all alloys.
Similar twists to failure were again
observed in all alloys albeit at lower levels
as for the unaged material.
The trend of reduced reverse bends with
increased boron levels is again observed
in the aged condition and about one bend
less is obtained in the aged condition
versus the unaged condition for all steels.
This suggests that the boron alloying does
not affect ductility significantly at the
levels of nitrogen investigated.
It should be noted that the nitrogen levels
of the present heats of approximately
40ppm are on the lower end of industrially
produced material.
Conclusions
The effect of boron alloying of 0.80C steels
to tie up “free” interstitial nitrogen was
investigated.
Heats with B:N ratios of 1.4 and 2.4 in
addition to a base alloy without boron
were laboratory prepared, hot-rolled,
drawn, patented and further drawn to a
final diameter of 1mm.
Microstructural
characterisation
was
conducted and tensile properties were
assessed.
Base
High B
B
Base
high B
B
Strength, MPa
Strain, %
a)
Strain, %
b)
Stress, MPa
▲
▲
Figure 5
:
Stress-strain curves of wire a) drawn to 2.5mm and b) patented at 2.5mm
UTS, MPa
UE, %
TE, %
Drawn to 2.5mm Base
1644
1.2
1.5
B
1592
1.0
1.1
High B
1677
1.2
1.5
Patented at 2.5mm Base
1324
7.3
8.6
B
1317
6.7
8.9
High B
1277
6.7
9.1
▲
▲
Table 3
:
Tensile properties Ultimate Tensile Strength (UTS), Uniform Elongation (UE), and Total Elongation (TE) of
the wires drawn to 2.5mm and patented at 2.5mm
UTS, MPa
UE, % TE, %
Nt
Nb
Base
2106
1.1
2.1
41
12
B
2096
1.3
2.4
42
11
High B
2087
1.4
2.5
41
9
▲
▲
Table 4
:
Tensile properties Ultimate Tensile Strength (UTS), Uniform Elongation (UE), and Total Elongation (TE) of
the wires drawn to 1mm after patenting
UTS, MPa
UE, % TE, %
Nt
Nb
Base
2263
0.4
1.5
35
11
B
2283
0.4
1.5
36
10
High B
2257
0.4
1.5
36
8
▲
▲
Table 5
:
Tensile properties Ultimate Tensile Strength (UTS), Uniform Elongation (UE), and Total Elongation (TE)
assessed following aging at 150 ºC for one hour of the wires drawn to 1mm after patenting