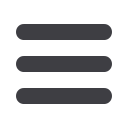

EuroWire – Mai 2012
72
Technischer artikel
▼
▼
Bild 1
:
Lichtoptische Mikrofotografien der warmgewalzten Stäbe aus Basis-, B- und hochborhaltige Stählen. Muster
quer gegenüber der Walzrichtung entnommen, in der Mitte des Querschnitts, geätzt mit 4% Pikral
▲
▲
Bild 2
:
Elektronenmikrograph-Übermittlung des
warmgewalzten und luftgekühlten hochborhaltigen
Materials
Basis
B
Hochbor-
haltig
die Wirkung des zusätzlichen “freien”
Bor bei mikrostruktureller Entwicklung
sowie mikrostrukturellen Eigenschaften.
Die Zusammensetzung der im Labor
vorbereiteten Gußblöcke ist in der
Tabelle 1
dargestellt. Dabei sollte beachtet
werden, dass die Verhältnisse in den
Zusammensetzungen im Gusszustand
(as-cast) etwas höher lagen als entworfen,
bzw. 1,44 und 2,39 je in den bor- und
hochborhaltigen Legierungen. Freies Bor
könnte daher auch in der Borlegierung
vorhanden sein.
Die Gußblöcke wurden auf einer manuell
beschickten Walzstraße warmgewalzt mit
einer Erwärmung bei 1176°C und einer
in drei Stufen auf zwei Warmwalzstraßen
durchgeführten Reduzierung. Anfangs
wurden die Vierkantstäbe von 12,7 auf
9,5cm mit abgerundeten Ecken (RCS -
Round Corner Square
) reduziert, gefolgt
von der Luftkühlung zur Raumtemperatur,
Erwärmung undWalzen auf 4,76cm.
Das Material wurde dann mit Maschinen
bearbeitet um Oxide zu entfernen und
in 6‑7 Blöcke geschnitten. Die letzte
Reduzierung wurde auf einer zweiten
Warmwalzstraße durchgeführt bis zu
einer Endgröße von 7,1mm. Das Material
wurde nach dem Warmwalzen bis zur
Umgebungsluft gekühlt.
Danach wurde das Material, vor dem
Ziehen, mit einer Säge auf Längen
von 3,7m geschnitten. Je Legierung
wurden
vierundzwanzig
Abschnitte
erzielt.
Obwohl
die
Thermo‑Calc
®
thermodynamischen
Berechnungen
ein Potential an Heißrissanfälligkeit im
hochborhaltigem
Stahl
vorhersagten,
wurden keinerlei Brüche noch wesentliche
Oberflächenmängel beobachtet. Während
eine wesentliche Entkohlung bemerkt
wurde,
8
wurde das Material auf 5,5mm
Durchmesser spitzenlos geschliffen.
Die
warmgewalzten
Stäbe
wurden
dann für die Kohlenstoff-Segregation
bewertet und nur Stäbe mit einem
Kohlenstoffgehalt von 0,78 ± 0.01
Gewicht-% wurden für das weitere
Drahtziehen ausgewählt.
Das
Drahtziehen
wurde
im
technologischen Forschungszentrum von
Bekaert durchgeführt und umfasste eine
Reduzierung von 2,5mm Durchmesser
in acht Ziehschritten. Die Patentierung
erfolgte dann in Salzbädern mit einer
Erwärmung auf 980ºC gefolgt von 520ºC.
Der patentierte Draht wurden dann
weiterhin auf 1mm gezogen.
Die Zugprüfung wurde an einer elektro-
mechanischen Zugmaschine bei einer
konstanten
Dehnungsgeschwindigkeit
von 5,6 10
-4
/s, mit einem 5cm
Dehnungsmesser bei 50% durchgeführt.
Zwei Muster wurden je Bedingung
geprüft.
Gleichmäßige
Dehnungen
wurden als technische Dehnung bei
der Spitzenlast, die für Zerreißfestigkeit
(UTS
-
Ultimate
Tensile
Strength
)-
Berechnungen benutzt wurde, bestimmt
und die gesamten Dehnungen bis zum
Ausfall wurden von den Angaben des
Dehnungsmessers
beim
Endbruch
erreicht.
Es wurde beobachtet, dass alle Muster
innerhalb der spezifizierten Länge des
Dehnungsmessgeräts versagten, wenn
nicht anders angegeben.
Die mikrostrukturelle Charakterisier- ung
erfolgte über eine lichtoptische Mikroskopie
geätzt mit 4% Pikral Muster und durch
Transmissionselektronenmikroskopie (TEM)
an einem Philips CM120 120kV-Gerät. Dünne
Folien wurden mit einem Doppelstrahl-
Schleifer Fischione elektropoliert, der bei
32V und bei Raumtemperatur arbeitet, mit
Einsatz eines Gemischs von 95% Essig- und
5% Perchlorsäure.
Dilatometrie wurde auf einem Gleeble
®
1500-System
durchgeführt.
Muster
wurden bei 950°C bei einer konstanten
Aufheizgeschwindigkeit
von
20°C/s
erwärmt und isothermisch fünf Minuten
lang gehalten. Der Stahl wurde dann
im
Heliumgas
bei
programmierten
konstanten Kühlgeschwindigkeiten von
je 50, 30, 25, 12,5, 10, 7,5, 5, 2,5 und 1°C/s
gekühlt.
Aufeinander folgende Prüfungen wurden
auf eine einzelne Probe je Legierung
durchgeführt. Die Dilation der Muster
wurde in Bezug auf Temperatur und
Zeit überwacht.