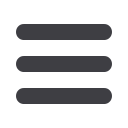

J
uly
2008
www.read-tpt.com98
›
I
n a mature industry, year-to-year advances are
often gauged by the number and sophistication
of simultaneous inline fabrication processes that
can be comfortably accommodated.
Advances are measured by the extent to which
the finest automated machinery enhances the
contribution of these operations to the finished
product. This is even truer in the area of tube mills
and rollforming lines, where Swiss army knife
versatility is an increasingly important factor.
Cut-to-length is the aspect of tube manufacture
that may be taken for granted. But pre-notching,
pre-punching, and post-punching are true ancillary
processes that expand the concept of rollforming
even as they add new lustre to the term ‘value-
added’.
These are not add-ons in any sense. They are
precision procedures in their own right, minutely
calibrated with
the main event:
production of the roll formed sections. The roll dies bend the
metal into shape. The pre-punch dies and pre-notch dies,
between the entry side of the roll former and the coil
reel directing the feedstock, perform
their own separate but equal functions.
As the finished sections exit the line, the
post-punch dies complete the fabrication
cycle.
Like rollforming lines, welded and seamless tube
mills are magnificent workhorses that are primed
for optimum production. Both sets of machinery
carry out an exquisitely orchestrated collaboration
that is, of course, continuous and accomplished at top
speed.
Anything else would be unthinkable – not to say ruinous to
productivity and, by extension, the plant’s bottom line.
F
ocus on
T
ube &
P
ipe
M
ills and
R
ollforming
L
ines
Both sets of
machinery
carry out an
exquisitely
orchestrated
collaboration
❱
❱