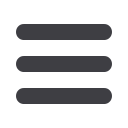

T
ube &
P
ipe
M
ills and
R
ollforming
L
ines
J
uly
2008
www.read-tpt.com102
›
EZTM has undertaken a range of
high profile projects including the
reconstruction of an electric tube-
welding mill (1020), which is in operation
at the Vyksa Metallurgical Plant. Such
reconstruction provides a capability for
rolling single-joint welded pipes with the
diameter of 1,420mm and wall-thickness
up to 48mm.
The company has also designed and
supplied a nine-stand sizing mill, which was
supplied to the Izhora Pipe Plant. The mill
is intended for a reconstructed tube rolling
plant (140).
A three-high rotary piercing mill,
installed on the line at a tube rolling
plant (80), has been manufactured
and put into service at Seversky Tube
Works. The mill can now operate with
156mm diameter sections, as supplied
by Seversky Tube Works, instead of
wire rod.
A unique piercing mill manufactured by
EZTM JSC for Seversky Tube Works has
been installed on a line of a tube rolling
plant (350) with pilger mill.
The mill – put into service in April of 2007 –
is intended for piercing F-sections with the
diameter of 360-400mm, as produced by
Seversky Tube Works.
EZTM JSC is one of the leading
designers of cold rolling mills with more
than 50 configurations intended for
production of tubes from 6-450mm in
diameter.
The company has manufactured equipment
for reconstruction of a cold rolling mill (32)
operating at the Nuclear Fuel Complex
(NFC), India.
In addition, EZTM has manufactured three
sizing mills, equipment for reconstruction
of a tube rolling plant (50-200), 15-stand
reducing mill and other equipment for TMK
and many other works in Russia and the
Ukraine.
EZTM JSC has built an excellent reputation
for the design and supply of new machinery,
together with the reconstruction of tube
plants operating in Russian tube works and
abroad.
Electrostal Heavy Engineering Works
(EZTM)
– Russia
Fax
: +7 496 577 7342
:
eztm@eztm.ruWebsite
:
www.eztm.ruprocessing equipment and spare parts.
All of the company’s equipment is certified
according to ISO 9001:2000 from the British
Standards Institute.
Electrostal Heavy Engineering Works
(EZTM) JSC, Russia, is involved in
the design and manufacture of high
quality rolling, blast furnace and mineral
Linear cage forming on tube mills
Olimpia 80, Italy, is a leading company in the design and production
of complete tube mills. Based on substantial experience of tube
requirements, the company has developed a new project for the
fastest change of forming rolls.
This tube forming system makes use of the latest technology
that allows the user to vary the diameter of the produced
tube without changing rolls. Olimpia 80’s unique
compact system consists of 8 sequential stations –
6 operating as breakdowns and 2 operating as
fin passes. These stations help achieve a final
and almost complete joining of
the tube.
Computerised servomotor opera-
tion is used on the 14 indepen-
dent axes of rolls positioning for
each breakdown and the 13
axes of every fin pass. This
helps to obtain, in a quick
and easy way, an optimal
position for the correct tube
forming. The strip feeding is assured by a system of independent pinch-rolls, mounted
on the first 6 stands.
The major advantages of this method are the greatest flexibility, the fastest automatic
change of tube size and the extreme reduction of roll costs.
Olimpia 80 Srl
– Italy
Fax
: +39 0523 864584
:
olimpia@olimpia80.com•
Website
:
www.olimpia80.com
A diagram of the linear
cage forming system
from Olimpia 80
Leading projects for EZTM tube and pipe rolling mills
A tube-reducing mill from EZTM