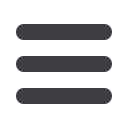

T E CHNOLOG Y
58
MARCH 2017
Innovative orbital welding process
THE choice to automate the welding
process occurs for various reasons
– technical, organisational and
economical. Many agree that this is the
ideal technique for obtaining clean and
smooth welds.
High-end industrial sectors like the
aerospace industry, high-speed trains,
nuclear or biotechnology lean towards
it for obvious reasons of precision and
dependability. In other areas, like in the
pharmaceutical and chemical industries
and in agribusiness, smooth welds are
indispensable so as to avoid all risk
of contamination or the possibility of
corrosion in the area of the weld.
Automated orbital welding involves
rotating continuously at 360
o
in an arc
around a cylindrical shaped form. This
is the best technical means to get clean
welds, with uniform precision particularly
for small diameters of thin widths. It
allows for thrust control of the process
with the help of the programming of the
welding settings. To ensure work without
irregularities, both on the inside and the
outside of the tubes, it is advisable to
choose automation for smooth welds.
Axxair has launched its latest
generation of orbital welding power
sources – a new technology to
simplify the orbital welding process for
applications in industries working with
thin walled stainless steel tubes. The
easy-to-use product is endowed with
an extensive range of possibilities.
Users have access to sophisticated
functions allowing them to perform
the most difficult welds with ease. The
SAXX suggests the control of the gas of
the torch or weld head, but also of the
internal shielding gas of the tubes. The
gas flows are, for the first time, displayed
digitally and are recordable. The system
controls and records welding data every
second. This data is stored on a USB
stick and can be transferred to DMOS/
QMOS records via the ‘Weldreport’
software.
It also allows the management of
the residual ppm inside the tubes to
guarantee a level of colouring of the
interior of the weld. The measurement
of ppm is carried out by connecting the
SPPM-10 from Axxair to the SAXX.
The software HMI as well as the
general software can be updated by
USB key. One USB stick can store up to
200 welding programs.
Axxair
– France
Fax: +33 4 75 57 50 80
Email:
commerce@axxair.comWebsite:
www.axxair.comClean, smooth welds from Axxair