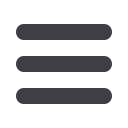

ECONOMIC REPORT
2016
70
• Nexen has improved the efficiency of its safety briefings to the 1,000 or so new workers, known as ‘green hats’,
who work on its North Sea assets each year. It has created a ‘buddy system’ of seasoned and new contractors
working together for more rapid and effective dissemination of information. Non-productive time associated
with ‘green hats’ has been reduced by 11 per cent and saved approximately £500,000, as well as delivering
improvements to safety.
The
Oil and Gas Continuous Improvement Network
, established in September 2015, has been brought under the
banner of Oil & Gas UK and the ETF and expanded to include efficiency champions across industry. The network
identifies success stories and challenges from the industry and shares them on the REE platform, supporting work
to embed changes in behaviour across the sector.
The ETF proposes to run a series of
Efficiency Roadshows
in company offices as away to engage theworkforce in the
pan-industry efficiency drive. These roadshows will be rolled out to Oil & Gas UK member companies throughout
the remainder of 2016 and into 2017.
8.2 Business Process
The
Inventory Rationalisation
project enables companies to share a virtual pool of resources so that they can reduce
their individual stock holdings and the costs associated with their storage and maintenance, as well as cut lead times for
access to vital equipment. Twenty-one companies so far from the oil, gas, construction, chemical and food processing
sectors are sharing information about over 200,000 inventory items on an online trading platform developed by
Ampelius Trading. It holds items ranging from valves and drill bits to gas turbines and subsea equipment. A number of
successful trades have now been facilitated through the system.
In the
Compression Systems
project, a group of operators who are accountable for the bulk of compression systems
outages on the UKCS – the main cause of unplanned maintenance – are working together to reduce the number and
duration of outages. As well as workshops to discuss best practice in this area, an industry guideline document for gas
compression operations is being developed.
Two additional projects have started this year to address inefficiencies in
procurement
and to further optimise
logistics
operations. A work group comprising operators and contractors is exploring opportunities to simplify and standardise
the tendering process. Within logistics, a test case in the Mariner Area is examining how operators can collectively
optimise helicopter and vessel movements. The ETF is also championing work by Oil &Gas UK to optimise
maintenance
as part of a drive to continuously improve major accident hazard management, and, in turn, operational efficiency.
8.3 Standardisation
The
Subsea Technology
work group comprising 30 companies has been analysing the potential cost savings from
carrying out projects to existing industry standards rather than bespoke requirements. It has identified that
savings of up to 30 per cent are possible. To share these findings, operator engagement sessions were held in
May 2016 in Aberdeen and London. The next steps are for operators to consider how they can adopt the learnings
within their own organisations and explore how standardisation could be applied to specific case study projects
to make them economically viable.
The
Valves
group is exploring how companies can work together to reduce the costs associated with valve
maintenance and supply across the basin through standardisation and simplification. Analysis of current costs in
the basin revealed that savings of up to 30 per cent are possible. These findings will be investigated by assessing
industry case studies in quarter four 2016.