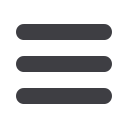

Wire & Cable ASIA – September/October 2009
32
inspections to look for damage to certain parts of carbon
fibre-reinforced plastic rudders on Airbus A330 and A340
wide-body aircraft.
The
Journal
article, to which Daniel Michaels contributed,
concluded by recapping a March 2005 incident in which
the rudder of an A300 flown by Canadian airline Air Transat
ripped off in mid-air: “The pilots managed to land the aircraft
safely. But subsequent inspections revealed that leakage or
fluid inside certain composite parts on some Airbus models
could damage rudders by undoing the internal bonds
between carbon fibres.”
Whatever the cause of Boeing’s troubles,
its supply line shall be held blameless
Staff writer Andrea James of the Seattle
Post-Intelligencer
reported on a notable feature of the Boeing Co factory
in Everett, Washington: the high-tech operations centre
overlooking the floor on which Boeing’s 787 Dreamliner was
being readied for first flight this summer.
[As noted above,
the event had to be scratched.]
The purpose of the new centre, which houses “about
three times as many flat screens as people,” is likewise
threefold: to monitor production of the big plane maker’s
suppliers around the globe, to solve problems quickly, and
– most essentially – to keep the 787 programme advancing.
(“Boeing’s 787 Production Is Mission-Controlled,” 30
th
April)
By name and by nature the new 787 Production Integration
Center is oriented to the Dreamliner, for reasons sum-
marised by Ms James. By this past spring the airplane’s
development was two years behind schedule, delayed by
parts shortages, labour troubles, and faulty communication
with Boeing suppliers worldwide.
About 70% of the 787 is built by companies other than
Boeing. Final assembly is at Everett, but production on three
other huge Boeing aircraft also takes place at the plant.
Coordination is an imperative if the 787 is to be ready for
delivery next year, after its several postponements.
According to Bob Noble, vice president of supplier
management for the commercial airplanes division of
the Chicago-based parent company, before building its
round-the-clock Everett centre Boeing studied a number
of seven-day/24-hour operations – including the National
Aeronautics and Space Administration (NASA) Mission
Control Center, in Houston, Texas.
Until the Boeing centre was functional, problems at Everett
took days to be resolved as emails bounced among time
zones. Mr Noble said, “We needed to take advantage of
the night.” According to the
Post-Intelligencer
, the 5,100ft
2
centre – which offers translator services in 28 languages
– is designed for quick response to production problems
wherever they occur.
The largest conference room, located in the former crane
pass-through area above the factory floor and fitted out with
cameras, is called ‘Dream.’ (Three other conference rooms
are known as ‘Perseverance,’ ‘Courage,’ and ‘Resolution.’)
But there is nothing whimsical about the design of the
centre, or its procedures.