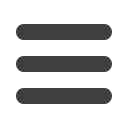

improves our industry-leading aftermarket
parts distribution network across the
region. The initiative is another example of
our close collaboration and partnership with
Barloworld Equipment by leveraging our
parts inventory data to significantly improve
the Caterpillar customer experience,” says
Chris Monge, manager of Caterpillar’s
southern African office in Johannesburg,
South Africa.
According to Bonnie Fetch, Cat Parts Dis-
tribution director, the increased collaboration
between Barloworld Equipment and Caterpil-
lar gets replacement parts to customers in
the region as quickly as possible. “This is ex-
tremely important as it allows our customers
to reduce idle time and save money. When
our customers win, we all win.”
Caterpillar’s operations were planned to
open doors in the second quarter of 2017. At
the time of writing, Barloworld Equipment’s
operations were due to commence early in the
third quarter of 2017. Barloworld Equipment
will occupy a surface of 3 500 m² of the
60 000 m² Caterpillar Distribution facility.
Further investments
Officially opened in February last year,
Wirtgen SA’s R50 million new facility in
Pomona was part of the Wirtgen Group’s
on-going investments into several capital
projects in the global market, driven by the
group’s “Closer to our customers” motto.
Speaking at the official opening, Jürgen
Wirtgen, president of theWirtgen Group, said
the group recently invested billions of Euros
into the expansion of its various facilities and
factories internationally to improve service
to customers. “For us, it’s not only important
to sell machines, but to be able to provide
first-class service and training as well.”
Wirtgen SA previously occupied a
2 500 m² piece of land and the new facility
occupies a massive 20 000 m². Office space
has been increased from 860 m² to 2 500 m².
Overall, the new facility represents a
massive 300% increase in space.
“It’s a step forward for us. It’s a new
chapter in our history. We have essentially
tripled warehousing and storage space and
dramatically increased the maintenance
workshop capacity. That allows us to better
service our customers,” says Schulenburg.
“We have also created more space in
the yard to be able to stock more relevant
products and maybe even products that
have never been available for this market
before. We have set ourselves some
ambitious targets. Even though the market
is in a declining phase, we believe we can
increase our market share.”
Meanwhile, the Volvo Group South-
ern Africa’s investment into an upgraded
R60 million integrated regional parts distri-
bution centre in Boksburg, Johannesburg,
South Africa in 2015 was meant to facili-
tate speedy parts deliveries, more stream-
lined and efficient operations, as well as
increased warehousing capacity for Volvo’s
brands, according to Torbjörn Christensson,
president of the Volvo Group SA.
“As Volvo Group SA, we believe that the
merger of our warehouse facilities under
one roof will enable us to better support the
company’s future growth within southern
and East Africa,” said Christensson, at the
time of the launch. “It is therefore a strategic
investment in our future and will enable us
to support our customers more efficiently and
timely, especially in light of the significant
volume growth our brands have experienced
over the last couple of years.”
The integrated parts centre is an upgrade
of the old facility. Storage area was
increased from 4 500 m² to 13 000 m².
Height of the building was also increased
from 7 m to 8,5 m. The Volvo Group SA’s
new regional parts centre consolidates
previously three different facilities, and has
significantly reduced logistical costs.
b