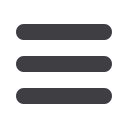

4
Mechanical Technology — May 2016
⎪
On the cover
⎪
W
PP was originally brought
into being in 1963 by
Peter Bahlig, following his
arrival in South Africa af-
ter leaving East Germany. In the 1980s,
the company was an early adopter of
laser cutting technology, which quickly
led to its pioneering role in the design and
manufacture of sheet metal enclosures
for the electrical industry.
The company was run as a fam-
ily business for over 50 years, with
Peter Bahlig at the helm until
his death in 2008. “I joined in
November 2013 after Peter’s
wife, Elizabeth, passed away.
The family link continues, though,
through their son, Mark, who
remains part of our leadership
team,” says Görtzen.
With a background in mechanical
engineering, Görtzen was immediately
charged with modernising the business
to restore market share in increas-
ingly tough economic conditions. “We
analysed every aspect of the business in
order to identify what processes could
be streamlined, where we could work
smarter, where we could improve effi-
ciencies and where we could save time
and money to offer our customers the
best value,” he says.
The company’s extensive sheet metal
processing operations – CNC laser cut-
ting, punching, bending, MIG and TIG
welding, powder coating, gasketing,
CNC milling and turning and assembly,
as well as electroplating, tool making, die
casting and plastic injection moulding –
used to be spread across five different
factory sites. “This comprehensive set of
capabilities sets us apart from our rivals.
While anyone with a bending brake and
a punching machine can make an enclo-
sure, because of our capabilities, experi-
ence and expertise, we are able to offer
far more in terms of added services and
in-house capabilities,” notes Görtzen.
Citing gasketing as an example, he
Sheet metal enclosures:
SA’s benchmark manufacturer
World Power Products (WPP), with over 50 years of experience in sheet metal
manufacturing, has modernised and repositioned itself to best meet the needs of an
increasingly competitive marketplace.
MechTech
visits the company’s newly streamlined
facilities in Johannesburg and talks to managing director, Jan Görtzen (left).
An overview of WPP’s dedicated punching area in the
sheet processing facility.
Inset:
A Trumpf CNC punching
machine being used to a perforate a panel.
says that many competitors offer stick-
on gaskets, “but ours are polyurethane
foam gaskets fitted during the manufac-
turing process using our CNC gasketing
machine. These are an integral part of
our designs and give us a genuine IP65
ingress protection rating for every enclo-
sure,” he says, adding that IP65 certifies
that the enclosure isolates live wiring and
moving parts and is ingress-protected
against dust and water sprayed from a
hose or nozzle.
WPP is also the only enclosure
manufacturer that makes its own locks
and hinges. “Over the years, we have
developed a robust range of locks that
have been widely copied overseas. Even
compared to these modern imports,
though, ours remain as good as you
can get in terms of value. They meet
all client expectations, including price
expectations, and are even used in the
enclosures manufactured by competi-
tors,” Görtzen tells
MechTech
.
To gain better control and to stream-
line its manufacturing processes, WPP
consolidated its manufacturing opera-
tions into two adjacent properties in Side
Road, Turffontein, Johannesburg. “This
has given us better control over our
processes, which has resulted in faster
turnaround times for our customers,”
he says. “We have become a much
leaner operation with all our resources
streamlined to maximise productivity and
minimise idle time,” he adds.
Dedicated punching, laser cutting and
bending areas have been established to
improve process control and material
flows. Sheet material deliveries now di-
rectly enter the sheet processing facility,
where the laser cutting and punching pro-
cesses are completed. Flat components
are then moved across to the second
factory, with the CNC bending area at
its starting point. Welding, grinding and
– downstairs from there – powder-coating
processes are completed in this facility,
followed by assembly. “We also have
a separate plating plant, along with a
machine shop – for components such as
pins, fasteners and busbars – which are