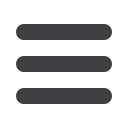

34
¦
MechChem Africa
•
January 2017
W
ith increasing urbanisation,
the 20
th
century introduced
process plants to mass-pro-
duce pharmaceuticals, food
and beverages, focusing on optimising cost,
time to market and reliability.
The21
st
centuryprocessplantisfacedwith
more complex needs. The triple bottom line
requires a solution involving people, prosper-
ity and the planet, with its finite resources,
particularly water.
Process plants concerned with products
forconsumptionarerequiredtomeetincreas-
ingly robust legislation demanding reduced
(or zero) bacterial/spore counts in the final
product.
The challenge is how to manage the
fabrication of new plants and maintain the
old plants to accommodate these changing
operating conditions.
Hygiene is often seen as both as a reputa-
tion and market risk, and as a costly alterna-
tivetocurrentpractices.Realistically,hygienic
welded fabrication will be more challenging
and more costly.
Whilst this puts capital budgets under
pressure, it should ease operational costs, en-
hance productivity and reduce clean-in-place
(CIP) andwater needs. The strategic choice is
business value and risk-driven.
Process plant construction
Process plants include a variety of, typically
stainless steel, components including factory-
made tanks, heat exchangers, columns and
pumps. These are interconnected by pipes.
During construction, fabricated components
are transported to site for assembly. These
are linkedonsiteusing thin-walled (wt<3%D),
small diameter piping. Connection is usually
by welding.
In the first ‘Materials engineering in practice’ column for 2017, Tony Paterson from the School of
Chemical and Metallurgical Engineering at Wits, talks about the work being done to ensure that the
pharmaceuticals and food-grade products coming out of our process plants are safe to ingest.
Left:
The ideal orbital weld for minimising Biofilm formation.
Right:
A manual weld taken from
an operating pharmaceutical plant. This weld is unacceptable by any sanitary standard.
Pictures courtesy of JD Cluett: www.arcmachines.com
Materials engineering in practice:
Hygiene and the process plant challenge
Most connecting pipes are measured
on site, ends prepared, aligned and welded.
Internal weld imperfections in small-bore
pipework are generally inaccessible. Site
welding requires skill, is more difficult to
control, and more difficult to manage for a
variety of reasons.
Biofilm formation and control
Complete sterility of plant, input materials
and water, whilst not a realistic expectation,
is the ideal. In the absence of complete steril-
ity, other methods need to be considered for
plant constructionor refurbishment practices
toeliminateormitigate against bacterial load.
Private sources of water have declined.
Municipality suppliedwater is of inconsistent
quality over time and product inputmaterials
are often shipped fromsources far away from
the process plants.
Biofilms form on exposed surfaces of pro-
cess plant as thin layers of microorganisms
adhering to surfaces. These may be organic
or inorganic, together with the polymers that
they secrete and biofilms can include harmful
bacteria.
Biofilm depth increases with increased
surface roughness, increased temperature
and lower flow speeds and is, therefore,
promoted by occluded and dead areas. One
source of surface roughness and local occlu-
sions are welded joints.
Resulting frombiofilmformation, bacteria
can grow and be released into the product.
Welded joints support biofilm growth
where there is:
• Inadequate penetration – the inner weld
profile leaves crevices (dead areas).
• Over penetration or cauliflowering – the
inner weld profile is proud (dead areas).
• Porosity.
• Cracks.
• Misalignment during manufacturing or
fabrication – occluded areas.
• Surface roughness due towelding process
effects across the width of the heat af-
fected zone (Laser < CMT < TIG/MIG).
CurrentlyCIPmethods areused to reduce the
impact of biofilms, but CIP is not completely
effective as:
• The loss of heat and chemical concentra-
tion over distance reduces effectiveness.
• The process does not clean hidden and
occluded areas.
• CIP requires the extensive use of water.
Manufactured pipes
Manufactured pipes are oval and bow to a
greater or lesser extent. Whilst accepted tol-
erances exist, the impact on welded joints is
significant particularlywith thinwalled pipes.
Pre-programmedorbitalTIGweldingisthe
preferredmethod of joining pipes. It assumes
well-matched faying surfaces because:
• The pre-programmed controlling current
and travel speed has to allow for the im-
pacts on themoltenweldmetal of internal
inert gas pressure, gravity and theoverlap-
ping wall thickness.
• If the faying surface overlap varies, the
current will be either too high or too low
leading to incomplete fusion or to over-
melting leading to poor weld geometry.
Research
Initial research used
E-coli
build-up to char-
acterise the effects of weld processes and
joint geometry. More recent research based
on real plant pipe analysis and a pair of math-
ematical algorithms using an 80% minimum
criterion as suited to orbital welding showed
poor results if randomly aligned, but better if
aligned through themajor axis. This indicated
the likelihood of bacterial build-up at joints.
Whilst the results were far better with
tightertolerances,movingtoahigherstrength
material witha thinnerwall thickness showed
the desirability of extremely low tolerances.
This places huge challenges on manufactur-
ing costs.
Current research is concentrating on site-
based methods of achieving closely matched
faying end surfaces using plastic forming ap-
proaches. The intent is to check effectiveness
using
E-coli
build up as the rating criteria.
q