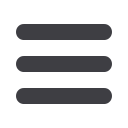

31
CONSTRUCTION WORLD
AUGUST
2015
PROJECTS AND CONTRACTS
at the final level in order to provide a safe
working platform for the installation of the
foundation piles,” says Oldknow.
Choice of piles critical
Naturally the choice of piles in any geotech-
nical project is critical. “Given the depth of
the kaolin, Franki Driven Cast-in-Situ piles
(Franki piles) were preferred to Continuous
Flight Auger (CFA) piles as the more efficient
solution. This was mainly because the Franki
pile’s founding could be achieved at a shal-
lower depth by forming an enlarged base at
the toe of the pile,” says Oldknow.
He adds that the CFA piles (which were
used for the soldier piling) would have to
have been installed at a considerable depth
given the weak shear strength of the kaolin
and would have required the removal of
the spoil material from the final basement
excavation level.
Franki had a 35-week programme from
21 July 2014 to completion 27 March 2015,
which included the lateral support, bulk
excavation, dewatering and foundation
piling. “In spite of the normal Claremont
winter rains, which are always challenging
given the Kaolin soil conditions, we are on
time in terms of anticipated completion
date. In fact we have managed to provide an
earlier start for the building contractor by
giving partial handover of half the completed
pile layout, which allows the contractor to
overlap with our contract providing them
with a two to three week head-start on their
contract programme.
“While there have been many challenges
on this project, we have been able to move
ahead efficiently. The excellent relationships
we have with our client, professional team
and contractors have, of course, been critical
to the success of the project.
Frank Africa has an experienced design
and construct team, especially in this
geographical area. “In the face of severe
challenges we have successfully provided
a lateral support design and constructed
solution that we have developed over the last
15 years and more in the Cape Town area,”
concluded Oldknow.
The CPUT Student Residence was
constructed within the group’s design
and construct model, opening up an
additional 295 beds, it brings relief to the institu-
tions high demand for student accommodation.
The design, by MLH Architects, offers maximum
occupancy with only double bedrooms and
shared amenities with the students’ comfort
and safety taking top priority. Biometric access
control was installed to control building access
with common areas strategically positioned at
the corners of the building – offering students
the best panoramic views of the Mother City
and Table Mountain.
Statistics released by the Department of
Higher Education and Training at the end of
2012 indicated a backlog of approximately
200 000 university beds, and since then the
depart-ments prime focus has been on student
housing funding.
“The NMC Construction group further
strengthens its portfolio in this sector with
the recent award of a new six storey student
housing development earmarked for students
of the Nelson Mandela Metropolitan University
(NMMU). Valued at R47,7-million the PE1 Devel-
opment for private developer, Campus Key,
it is located in Summerstrand – Port Elizabeth.
“In addition to these projects, we have
commenced with construction of the new
R40-million Heimat Student Residence for the
University of the Free State in January 2015, with
works on the R187-million Ndumo High School
in KwaZulu-Natal progressing well,” says Mike
van Coller, NMC Group procurement director.
Recently completed projects in this sector
include the R229-million OBZ Student Resi-
dence for the University of Cape Town and the
16 000 m² NMMU Student Living and Learning
Housing Development for the Nelson Mandela
Metropolitan University.
Summary of scope of works
• 21 000 m³ bulk earthworks
• 1 870 m² of lateral support consisting of excavation
in 1,5 m stages in depth
• Soldier piling comprising 147 No. 500 mm Ø CFA
piles using a B125 Casagrande drill rig
• Construction of the concrete capping beam.
• Trimming and construction of gunite arches via dry-
mixed, air-driven guniting
• Installation of ground anchors and temporary steel
walers at designed intervals
• Installation of temporary dewatering system and
sacrificial piling platform
• Construction of temporary access ramp for
foundation piling rig access at base level
• Installation of Franki pile 600 mm Ø foundation piles
using a Franki British crawler piling rig
The perched water table had to be
constantly managed to ensure that the
in situ soils would not become saturated.
EXPANDING INTO EDUCATION
NMC Construction Group
Established in 1983, the NMC Construc-
tion Group is a multi-disciplinary
construction group with a national
footprint and SADC presence. Currently
the organisation has offices in Cape
Town, Johannesburg, Durban, East
London, Port Elizabeth, Kathu,
Springbok and Windhoek.
The business growth is attributed
to the NMC Construction Group’s
strategic intent to expand its market
space to include civils infrastructure
and to diversify its building portfolio
to include commercial, retail, bulk
residential and institutional and social
services sectors.
The NMC Construction Group’s
civils and building divisions are ISO
accredited in the following three ISO
standards; ISO 9001, ISO 14001, OHASA
18001. These entities have a level 2 and
level 3 BBBEE rating and a CIDB GB9
and CE8 grading respectively.
>
The NMC Construction Group’s building division, has successfully
completed a new R51,4-million student residence for the Cape
Peninsula University of Technology (CPUT). Students are expected
to occupy the residence in the third semester of 2015.