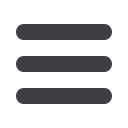

28
›
T
echnology
U
pdate
M
arch
2009
End-forming and bending technologies in a single unit
The machine is used for tubes
with varying diameter ranges from
6-22mm and lengths ranging from
130-800mm. The tubes pass a
one-sided transfer end-forming
process which enables complex
forming geometries with up to 6
axial forming steps and 1 rotary
forming step. The forming of the
opposite side takes place in a
separate transfer process with
4 axial forming stages and one
rotary forming stage.
After both sides are formed, the tube passes
through an optical measuring process,
which allows an integrated control
of the final forming geometries.
An additional handling system
forwards the formed tube to a
bending machine, which utilises
three fully electrical clockwise
working bending heads. The
bending heads are equipped with
a front adapter to support the end-
forming geometry in the bending
process and to facilitate the
first bend close behind the end-
forming.
A counter clockwise bending unit is
located above the three clockwise
bending heads. The unit is applied
German bending machine manufacturer transfluid’s next
innovation – the supercell – during the bending process
The transfluid supercell: six axial forming steps enable a more
complex end-forming process
to a guiding system, enabling the three
clockwise bending heads to produce one
or more counter clockwise bends. Further
bends can be produced with the clockwise
processing machines.
The machine can be equipped with an
optical control system, which verifies the
complete bending geometry after the final
bending process. Several functions and
positions, as well as the bending geometry
itself, can be programmed and adjusted via
an integrated touch panel.
TransfluidMaschinenbau GmbH
–
Germany
Fax
: +49 2972 97 15 11
:
info@transfluid.deWebsite
:
www.transfluid.deTransfluid, Germany, has created an
efficient and innovative tube processing
solution by arranging existing end-forming
and bending technologies into a single unit.
A benefit of this new machine is the direct
loading process automatically initiated by
a container, resulting in a fully automated
3-hour production process that requires no
manpower at all.
A specific demand during the conceptual
stage of this unit was to speed up the
final production process. The results are
convincing: both sides can be formed with
7 bends, and a tube can now be processed
within 6 seconds.
IMS Messsysteme GmbH, Germany, has
delivered a multichannel tube wall thickness
measuring system to Vallourec & Sumitomo
Tubos do Brasil Ltda (VSB), following an
order last year. The measuring system will
be used to measure tube shells at the exit
of the PQF mill (SMS Meer). The system
will be installed behind the PQF extractor
mill.
Apart from the well-established 13-channel
measuring geometry for PQF mills, which
is used for continuous measurement of
polygonal wall distribution, the measuring
system will be equipped for the first time for
VSB with a high-resolution diameter gauge.
A total of 18 laser triangulation sensors will
be fitted. This will enable highly accurate
detection of out-of-round flaws and profiling
of the tube outside diameter.
The laser-based measuring technology
integrated here for the first time in an IMS
IMS delivers new multichannel
wall thickness measuring system
tube wall thickness measuring system
has already been used successfully
for several years at Ovako Steel AB
in Hofors, Sweden, as a standalone
measuring system. The sensor and
analysis systems are now being
integrated in the IMS measuring system
in close cooperation with the company
LIMAB.
IMS can therefore simultaneously
measure the wall thickness and
eccentricity, outside diameter and
profile, temperature and length of tubes in
a single compact gauge. This avoids the
need to install multiple individual systems,
which means not only savings in the cost
of the overall investment, but also simpler
maintenance and upkeep.
IMS can look back on more than 20 years
of close cooperation with Vallourec &
Mannesmann Tubes, a member of the
Vallourec Group, at various locations
around the world and Sumitomo in Japan.
This new contract included, IMS has already
supplied this mill operator with more than
15 individual measuring systems.
IMS Messsysteme GmbH
– Germany
Fax
: +49 2056 975 140
:
info@ims-gmbh.deWebsite
:
www.ims-gmbh.de
A multichannel tube wall thickness measuring system
from IMS Messsysteme