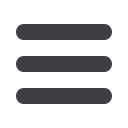

M
arch
2009
www.read-tpt.com32
T
echnology
U
pdate
›
Six axis CNC profile cutting machine
Shandong Fin CNC Machine Co Ltd, China, develops, manufactures and sells CNC
machines such as drilling, milling, punching, sawing, cutting machines and other optical,
mechanical and electronic integration equipment. The company tracks new technologies
and aims to make continuous innovation in technology for manufacturing high-grade
equipment, with a focus on the electric power, steel structure and automobile industries.
The company’s PB660 CNC profile cutting machine is designed for pipes within the
diameter range 60 to 600mm, of thickness from 2.3mm to 25mm, and in lengths from
600mm to 12,000mm. Maximum pipe weight is 5,000kg, the minimum intersection angle
is 20°, and the bevelling angle is from 30° to 150°.
The machine is equipped with a colour touch-screen and an air-plasma cutting machine
(OTC D-12000), and operates in six axes (workpiece rotating, longitudinal movement,
torch swing, torch adjustment, up-down movement and front-rear movement), with a
maximum workpiece rotating speed of 8r/min. The maximum distance of longitudinal
movement is 12,000mm, and the maximum longitudinal speed is 10,000mm/min.
Shandong Fin CNC Machine Co Ltd
– China
Fax
: +86 531 88875516 •
:
fincm-int@fincm.com•
Website
:
www.fincm.comSMS Elotherm, Germany, has won an order
from Tectubi Raccordi SpA (Allied Group)
that further strengthens the company’s
business relations with this renowned Italian
producer of pipe bends. Tectubi Raccordi
will receive an inductive heating plant for
the production of pipe bends (Ø 56") that
operates to the ‘Hamburg method’ and,
with an inductor power input of 2,400kW
and 1,600kW respectively, represents the
world’s most powerful plant of its type.
Commissioning was scheduled to start in
quarter one of 2009. The company’s
scope
comprises equipment for preheating the
still straight pipe section plus two medium-
frequency infeed units for heating the bent
pipe section. In addition, the order covers
three sets of inductors for the production
of pipe bends with diameters from 36"
to 56".
The heating plant will be designed for bends
of standard steel and austenitic grades,
and will be able to process pipes with wall
thicknesses of up to 60mm. The power input
of the first inductor amounts to 2,400kW,
while the bent inductor will be rated for a
maximum power input of 1,600kW.
The transistorized converters will be
equipped with an SMS Elotherm digital
control and are connected with the PLC via
Profibus facilities. Two temperature cameras
installed at the inductor outlets provide the
data for power setting as a function of the
pipe feed motion.
The ‘Hamburg method’ for pipe
bends production operates
according to pipe sections
being pushed over a mandrel
which has the curvature
required for the finished
pipe bend. The feed-forward
movement is accomplished by
means of a hydraulic press.
The pipe is heated in
two zones. Preheating is
accomplished in the straight
part of the inductor without
any material deformation or
forming, while the bent inductor
serves to heat the pipe to the
desired final temperature. It is here that
forming takes place.
Heated to final temperature, the pipe is
pushed over the mandrel by the press, and
thus takes the shape of the mandrel. This
method requires the mandrel to be heated
before production starts which is under-
taken by means of the bent inductor and the
associated medium-frequency infeed unit.
The ‘Hamburg method’ is suited to an array
of materials and stands out for the fact
that after forming the wall thicknesses are
nearly identical over the complete pipe. In
addition, the cross-section of the pipe bend
maintains the circular contour of the starting
pipe.
SMS Elotherm GmbH
– Germany
Fax
: +49 2191 891 726
:
m.oelmann@sms-elotherm.deWebsite
:
www.sms-elotherm.com
Fabrication of a 24" pipe bend with inductive heating
World’s largest inductive heating plant
for pipe bends
Skiving and roller
burnishing machine
Sierra Machinery Inc, USA, has launched
its new-generation Sierra USA
®
machines
and patented tooling. The Sierra USA
goes
to the highest level in finishing steel tubes
for the hydraulic cylinder industry and other
applications where fine-finishing of the
internal diameter of a tube is required.
Skiving is the preference over honing
by manufacturers worldwide such as
Caterpillar, Komatsu, Wipro India and JC
Bamford UK. The company is renowned as
being the manufacturer of the world’s fastest
skiving and roller burnishing machines and
patented tooling.
The Sierra USA offers greater speed,
increased cost efficiency, and high quality
machining solutions to serve the cylinder
manufacturing industry.
A skived and burnished surface provides
longer seal life and has a 50 per cent higher
TP rating than that of a honed surface.
On an example of 88.9mm bore tube
(762mm long), the Sierra USA can achieve
finishing in 30 seconds including loading
and unloading. This equates to 122 tubes
per hour, achieving H8 and Ra 0.1-Ra 0.4.
Skiving and burnishing is 80 to 100 times
faster than honing.
Sierra Machinery Inc
– USA
Fax
: +1 775 358 6739
:
sierram@sierramachinery.comWebsite
: Sierramachinery.com