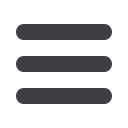

95
M
arch
2009
www.read-tpt.com›
H
andling &
P
ackaging
T
echnology
Today’s market requires every company
to ensure that the in-plant material flow,
storekeeping and movement of goods are
organised economically.
As many companies continue to experience
considerable pressure on prices and lead
times, the ergonomic planning of in-plant
material flow can lead to an immediate
reduction in costs.
Stierli Bieger AG, Switzerland, has
developed a new and unique roll-out
material storage system based on intensive
onsite research with a number of existing
customers. The main advantages of the
Stierli Bieger system are the improvement
in utilisation of floor space, tidy and
compact storage within the factory, and fast
and safe material handling.
In addition, downtimes of production
machinery can be minimised, and safe
working practices within the customer’s
company can be considerably improved.
By using this system, the company
claim to avoid the usual risks associated
with the stacking and storage of stock
materials.
The number of arms, width clearance,
single or double construction can be
individually selected. The arms can be
removed easily and safely by hand. The
synchronized system developed by Stierli
Bieger guarantees parallel running of
the arms with a loading capacity of up to
1,500kg/arm. The arms are equipped with
maintenance free grooved ball bearings.
Additional sheet metal channels or wood
supports can prevent damage.
Stierli Bieger is the manufacturer of roll-out
racks, devices for welding and dressing,
and horizontal bending machines.
Stierli Bieger AG
– Switzerland
Fax
: +41 41 920 24 55
Website
:
www.stierli-bieger.comA new hex bundling system, from
Automated Solutions Inc, will soon be
in production at a major US tube and
pipe supplier. The system will end align
tubes, build layers of tubes and stack the
layers into hex bundles. It automatically
straps bundles and accumulates finished
bundles on a conveyor for either crane or
fork truck removal.
The system will process 2" to 6" diameter
tubes (2
3
/
8
" to 6
5
/
8
" OD), wall thicknesses
of 0.109" minimum to 0.280" maximum,
and lengths from 16-44ft. Dual strappers
optimize cycle times, especially when
operating in dual stacking mode where two
shorter hex bundles (ie 16ft lengths) are
stacked and processed simultaneously.
The operator can
select tube diameter,
tube length, and
bundle configurations
from a touchscreen
HMI,
with
size
changeover being fully
automatic.
Servomotors are used
for their smoothness,
reliability,
clean
appearance,
and
flexibility for both the
horizontal
carriage
travel and the vertical
axis travel of the
stacking gantry.
Automated Solutions Inc is a global
supplier of custom automated equipment,
specializing in tube and pipe handling and
processing equipment. All mechanical and
electrical design, fabrication, assembly,
and testing is accomplished at ASI’s
100,000ft
2
facility located in Knoxville,
Arkansas, USA.
Tube and pipe equipment includes
automated tape bundling, end finishing,
hex bundling, cap and coupling systems,
specialized conveyors, and accumulation
devices. Standard machines include
designs for processing
1
/
4
" diameter to
6" diameter tubes and lengths up to 80'.
Layouts and system configurations are
flexible to suit customer needs.
Bar code applicators, weighing systems
and other peripherals can be added to
compliment systems. Installation and start-
up assistance is always available from
Automated Solutions.
Automated Solutions Inc
– USA
Fax
: +1 479 885 2085
:
sales@automatedsolutions.bizWebsite
:
www.asideas.com
The hex bundling system from Automated Solutions
Hex bundling system for swift packing requirements
Safe material handling in a confined area
The roll-out material storage system from Stierli