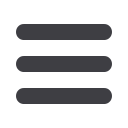

162
S
eptember
/O
ctober
2007
Advanced cleaning methods for tube and pipe:
tube super-cleaning
By Dott Chiara Di Pierro, Fismet Industriale Srl, Italy
1. Introduction
Tube and pipe is a necessary material for life and progress, and can
be supplied in a range of diameters and materials. It is available
in sizes across the spectrum, ranging from large dimensions for
booster, oil-hydraulic cylinder, and oil pipeline applications, to tiny
diameters for needles, capillary, and cannulae.
The use of tube is increasingly varied, with growing requirements
for products such as fibre optics and oil pipeline. In the future,
the use of tube is set to increase, with a whole raft of innovative
applications, such as goods transportation or high-speed trains
being enclosed in tube.
In order to facilitate the safety and smooth operation of these
applications – from old to new – it is vital to develop and implement
the most advanced tube cleaning methods possible. Fismet
Industriale Srl is dedicated to the production of industrial cleaning
systems and ultrasonic cleaning systems. In developing its
equipment and technology, the company aims to take the best care
of operator safety and environmental protection.
Due to the growing demand for industrial cleaning in manufacturing,
Fismet invests substantial resources into the research of advanced
and alternative cleaning processes. Fismet’s equipment range
includes:
• Super-cleaning machines
• Ultrasound systems
• Carbon dioxide machines
• Dry saturated steam high pressure generators
• Sandblastings
2. Effective cleaning for inner and
outer tube surfaces
In order to best utilise tube and pipe, it is necessary to achieve
perfect inner and outer tube cleaning. This is the case even at the
superficial boundary layer of tubes. However, the level of perfect
cleaning is not an absolute value good for every production sector.
Instead, it is relative and depends on the type of production field,
operating conditions and application of the tube. Therefore, the
best cleaning methods always take into consideration the end-use
in relation to the manufacturing phase in which the tube has to be
washed.
The purpose of a tube-cleaning machine is to entirely remove
lubricants used during manufacturing phases. These residuals
cannot be removed by a simple chemical immersion bath, because
contaminants are strongly fixed.
The requirement of perfect pipe cleaning treatment is essential
in the ultimate phase, but it can also be integrated into the
intermediate phases of the tube manufacturing process. In the latter
case of intermediate cleaning, the washing machine has to fit into
the manufacturing line without loss of productivity. This means the
washing machine should have no negative impact upon production
line efficiency.
The perfect cleaning of tubes allows the highest level of efficiency
and relies upon advanced equipment integrity. An increasingly
important
factor,
the
tube cleaning process is
becoming more difficult
because tubes are being
manufactured with more
complicated specifications,
either in dimension and
structure or constitutive
material.
›
Figure 1
:
Medical cannulae in stainless steel
fi
Figure 2
:
Copper pipe coil
€
Figure 3
:
Small tubes in different
metal for household
apparatus and appliances