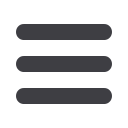

163
S
eptember
/O
ctober
2007
Furthermore, it is absolutely necessary to invest in research of
advanced cleaning technologies to take into account a range
of important issues. These include worker safety and health,
environmental protection, reduction of water and electricity
consumption, reduction of waste and use of ecologically compatible
chemical detergents. For this reason, it is necessary to always
develop machines with a totally closed cycle. It is also important
to develop accessories for cleaning equipment in order to avoid
any dispersion and to recover, filter and treat all fluids and vapours
produced by the cleaning process.
The excellent performance of a cleaning machine depends on the
coexistence of certain conditions. These conditions are advanced
technical features, an effective cleaning cycle, optimum working
temperature, and efficient chemical detergents. However, one
technology that can substantially improve performance is ultrasonic
technology.
In order to obtain the most effective ultrasonic action it is necessary,
first of all, to choose the best type of ultrasonic technology (eg
magnetostrictive or piezoelectric). Once this has been selected, it
is necessary to establish, for each particular case, the best setting
frequency, power, ultrasonic transducer shape, and ultrasonic
transducer dimension/position. These settings must all be achieved
according to liquid density and tube weight and shape.
3. The definition of tube ‘super-cleaning’
The main problem faced by all producers of industrial cleaning
systems, is the penetration of the superficial boundary layer on
tubes to be cleaned. This procedure is otherwise known as ‘super-
cleaning’. Contaminants are usually bound to the tube surface by
hard cohesion stresses, which are due to electrostatic phenomena
and contaminant chemical composition. The smaller the contaminant
particles, the more difficult it is to remove them.
There are only a few renowned methods used to penetrate the
boundary layer. The most effective are ultrasound technology or
the use of special fluids (eg carbon dioxide). In both cases, the
contaminant particles acquire the necessary energy to detach
themselves from the tube surface. However, this mechanical
removal action has to be added to a thermal action (either heat or
cold helps remove the contaminant).
Super-cleaning is gaining increasing benefit from the development
and implementation of mechanical actions such as ultrasound,
agitation, rotation, balancing, hydrokinetics, and spraying. In
addition, research and development into alternative detergent
solutions is also improving the effectiveness of super-cleaning,
especially since traditional solvents are regarded as dangerous for
health and the environment.
4. Precision requirements of medical
tube cleaning
The cleaning of medical tubes, needles and cannulae represents
a very complex and difficult washing problem, comparable with
human body prosthesis cleaning. During drawing and subsequent
manufacturing operations, the tube becomes dirty with oil and
grease, while metal porosity is also a problem. A number of tests
have proved that a washing cycle activated by ultrasound permits
Panel 1: Examples of very difficult tube
cleaning processes
In the panels on pages 163, 164 and 165 are cases of tubes
and tube cleaning machines representing the most difficult and
actual cleaning problems.
In the first panel (figures 11, 12, 13 and 14) the problem and
solution concerns the achievement of premium tube cleaning
under a high productivity output. The cleaning operations have to
be totally automatic and the machine is inline, strictly connected
with the manufacturing machine. The goal is more difficult when
the main manufacturing line has a high output per hour and the
cleaning cycle cannot delay production. Therefore, the cleaning
machine has to reach the best performance in a very short time.
€fi
Figure 11-12
:
Automatic equipment
(outer and inner) for
ultrasonic cleaning,
rinsing and drying of
aluminium tubes for
fumes discharge of
house heating plant
(productivity of 1 tube
every 30 seconds)
€fi
Figure 13-14
:
Automatic high productivity equipment
(outer and inner) for ultrasonic cleaning,
rinsing and drying of stainless steel tube
for pipelines.This machine is automatically
connected with the manufacturing
equipment