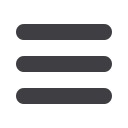

73
M
ay
2009
www.read-tpt.com›
As an international plant engineering and manufac-
turing company we provide you with expertise that
is backed by our extensive experience and our product
solutions to ensure an optimum utilization of your
production process. In everything we do, we have one
thing in mind: to help you best to achieve your goals.
Call us + 49 2372 506 0 or
info@siemens-seuthe.comMetals Technologies
Seuthe Tube Welding
and Section Lines
The bookshelf
Getting a firmer grip on metals costs in huge
capital projects
A
‘white paper’
available to registrants of the blog MetalMiner has
a long title:
‘Cost cutting ideas – reducing steel and related metal
costs in major capital projects for oil & gas and petrochemical
turnarounds’
. But it is succinct and persuasive. For anyone open to
the thesis that careful monitoring of costs can benefit both buyers
and sellers of metals on a large scale, it will reward the investment
in reading time. Registration is free at
www.agmetalminer.com.
The authors are Lisa Reisman and Stuart Burns, co-founders of
Aptium Global Inc, a Chicago-based consultancy in metals sourcing
and project management. Both have a background in trading metal
products around the world. In summary, they assert that companies
generate greater cost savings when they break out fabrication costs
from the underlying metal costs and track both sets of data over
time. Multiple strategies are recommended, and examples cited.
The last section,
‘Conclusions and savings,’
is attention-getting,
although the authors acknowledge that generalizations can be
misleading. Savings will vary across product categories (pipes,
heat exchangers, pumps) and volumes. The urgency of a particular
requirement can also impact savings.
Nevertheless, write Ms Reisman and Mr Burns,
“We have seen
savings,”
as follows:
• Steel tube 4-6 per cent
• Stainless tube 15-18 per cent (before surcharges)
• Flat rolled steel 9-11 per cent
• Flat rolled stainless 10-12 per cent (before surcharges)
Depending on the metal involved,
“more-processed and further-
worked products typically,”
yield similar results:
• Castings savings 4-11 per cent
• Fabrication savings 7-17 per cent
Oil and gas
Massachusetts, with 7,900 miles of antiquated
gas pipes in the ground, is calling for
replacement
Statistically, explosions from gas leaks are very rare in the United
States, where roughly 1.1 million miles of natural gas mains
crisscross the country. According to federal data cited by Boston
Globe staffer Keith O’Brien, such incidents are even less common in
Massachusetts: 20 events and six deaths between 1998 and 2008.
(Nationwide, over the past two decades, there were fewer than 90
incidents per year, and just over 15 fatalities annually). But several
recent explosions have prompted state officials to review the 12
incidents recorded in Massachusetts since 2004.
Mr O’Brien supplies a context for the obvious questions: Is the
state’s underground network of pipes as safe as it should be? Are
these terrifying events just part of the cost of a gas distribution
system? Could utilities and state regulators be doing more?