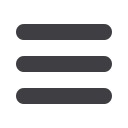

82
›
I
nspection,
M
easuring,
T
esting &
M
arking
M
ay
2009
The Varimac
®
eddy current comparator
and production comparator can be used
to check alloy, heat treat or hardness in
tube, It can also be used to sort parts
such as fasteners, bearings, pistons, strut
rods, and similar parts. MAC systems
can also incorporate a laser gauge where
only the outside diameter of the tube is a
concern.
For heavy wall magnetic OCTG such as
linepipe and casing, MAC’s Rotoflux
®
flux
leakage inspection system provides precise
detection of longitudinal and transverse
calibration notches or defects on the OD
and ID. These defects might include rolling
skins, laps, cracks, laminations, cavities,
and defects within the wall, along with drilled
holes specified for calibration. The Rotoflux
can handle diameters up to 406mm.
Several recent OCTG systems installed
in Europe and Asia have included MAC’s
220mm Rotoflux transverse and longitudinal
flux leakage systems, demagnetizers, and
Echomac UT (180mm or 220mm) to detect
defects and measure wall thickness.
Mechanical handling and feed systems
include articulating roll feeds or inlet and outlet
conveyors. These are composed of driven
V-rolls that feed the tube through a constant
centre triple guide bench and transport the
tube into accept or reject pockets.
Some of the materials being tested include
heavy wall, hot rolled, straight or upset
pipe and low-alloyed carbon steel, and
seamless tube with wall thickness up to
25mm. Automatic markers and a conductor
control panel complete the systems.
Magnetic Analysis Corporation
– USA
Fax
: +1 914 699 9837
:
jgould@mac-ndt.comWebsite
:
www.mac-ndt.comThe ‘Conductor’ control system operates all
functions of the line to allow for changes in
diameter, end suppression, handling and
sorting, plus data acquisition and network
accessibility with remote viewing.
This system was custom
designed to include 7
channels of Echomac
®
FD-4 ultrasonic electronics
with a 75mm UT rotary
test head to inspect
Ø 12.7mm to 76.2mm pipe.
Four shear wave channels
are included to detect
surface and subsurface
defects to normal industry
specifications such as API.
Three compression wave
channels are used for
delamination detection, and
ID/OD diameter and wall
thickness measurements.
Other MAC ultrasonic systems have recently
accommodated material diameter sizes from
6.35mm to 220mm with electronics up to 32
channels in a single chassis.
MAC’s eddy current test systems – such as
the Multimac
®
, Minimac
®
, or MAC400 – can
inspect automotive pipe for surface, subsur-
face, OD/ID cracks, and weldline defects,
including short transverse discontinuities.
Magnetic Analysis Corp (MAC), USA,
provides complex eddy current, flux
leakage, and ultrasonic, multitest systems.
With over 80 years of experience, MAC’s
technology incorporates test methods for
magnetic and non-magnetic metal tube,
bar, wire, plate and parts during online or
offline manufacture.
Automotive pipe and parts as well as oil
country tubular goods (OCTG) can be
inspected using MAC’s exclusive and
advanced NDT inspection systems. The
company offers eddy current systems to
detect short surface, subsurface, OD/ID
cracks, and weldline defects, including
short transverse discontinuities.
MAC also provides ultrasonic systems
for material defects such as longitudinal
and transverse cracks, inclusions, ID/OD
and dimensional changes such as wall
thickness, eccentricity and ovality. Flux
leakage systems are also available to
detect longitudinal and transverse defects
on the OD and ID, along with wall defects.
MAC has recently installed a large
ultrasonic (UT) inspection system at a
European tube mill that is designed for an
offline test of ERW carbon steel and other
automotive tube. This system has an inlet
and outlet conveyor for tube handling,
together with an automated constant centre
triple guide roll bench system.
Comprehensive test systems for automotive
and OCTG tube
The multi test 220mm Echomac
®
ultrasonic and Rotoflux
®
flux leakage test system is used to detect
transverse and longitudinal defects in OCTG tube up to 193.68mm diameter with wall thickness from 4mm
to 25mm
A 180mm Echomac ultrasonic inspection system to inspect hot
rolled, seamless carbon steel tube using 16 test channels to detect
longitudinal and transverse flaws and lamination