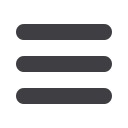

86
›
I
nspection,
M
easuring,
T
esting &
M
arking
M
ay
2009
Haven Manufacturing Corporation, USA,
has expanded its material handling and
systems control knowledge into the oil and
gas pipe testing market. The company
is a worldwide leader in integrated tube
processing systems.
In cooperation with a leading non-
destructive test company, Haven has
designed a gantry and rail system that
supports a full body phased array ultrasonic
tester. The capacity of this system is from
64-535mm diameter and up to 15m long.
A walking beam transfer device positions
the pipe in the test station, while
simultaneously removing a tested pipe.
In the testing station, the pipe is rotated
at a controlled rpm to match the specified
linear speed of the ultrasonic tester
carriage.
Multiple servo drives control the
test cycle synchronization, while
manipulation of up to 11,000kg of pipe
at one time requires both precision and
robust construction.
Haven’s reputation for dependable
design and superior quality has been
transformed from its standard tube
cutting and tube finishing products to
an industry that demands ultra-reliable
performance.
In addition, the company has also been
involved with pipe end-to-end manipulation
for ultrasonic testing.
Haven Manufacturing Corporation
– USA
Fax
: +1 912 264 9001
:
sales@havencut.comWebsite
:
www.havencut.comTUBETECH
CORPORATION
LIMITED
TUBETECH WUHU MANUFACTURING
CO.,LTD
Automated non-destructive testing systems
NDT Technologies Inc, Canada, is the manufacturer of a range of automated non-
destructive testing systems, precision measuring and material handling. The company
has launched a new device for offline detection of internal and external flaws in
automotive engine cylinder liners.
The system uses the eddy current flaw detection method for the detection of micro-
cracks, surface imperfections and sub-surface flaws. Defective parts are diverted to the
reject chute. Typical test cycle in production factory is less than 15 seconds.
NDT Technologies has also introduced an automotive hollow shaft flaw detector. The
Eddytron TM is designed to inspect aluminium steering column casting for internal
surface flaws in the body, and in the hydraulic seal seat chamber.
The casting is used for power steering applications in automotive industry. Due to the
operational importance and highly complex geometric shape of the cast part, stringent
quality control parameters need to be implemented. The system provides electronic
evaluation of changes in eddy currents (due to imperfections) that are present on
material surfaces.
The method is sensitive to changes in distance between the probe and the material,
requiring a high level of manufacturing precision on the probe guidance system. Flaws
as small as 0.2mm deep can be detected.
In order to achieve test consistency, the system is supplied with calibration specimens
that contain artificial flaws of known dimensions. The calibration specimens are used to
set the test base line sensitivity.
NDT Technologies Inc
– Canada
Fax
: +1 514 457 7652
:
info@ndt.ca•
Website
:
www.ndt.caEffective handling and ultrasonic testing of
oil and gas pipe
An ultrasonic tester using Haven’s gantry and rail system