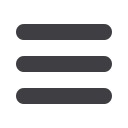

91
www.read-tpt.com›
I
nspection,
M
easuring,
T
esting &
M
arking
M
ay
2009
in order to find the true ‘pulse’ of the
process, which in mandrel bending exhaust
tubing is detection of the pull force during
the bend cycle.
Strategic placement of a piezoelectric
sensor captures representative force
feedback while remaining completely
clear of the business end of the machine.
Figures 1 and 2 show the pull force
captured during normal operation and
then when a typical process variance was
induced to demonstrate the effect on the
force involved; there is loss of lubrication
(figure 1) and misalignment in the setup
(figure 2).
An effective process variation monitoring
system comprises 3 elements: a sensor,
an intelligent control module and a
user interface. The PVM2000-MB™
mandrel bend monitor from OES utilizes
a piezoelectric strain sensor mounted
on the mandrel rod housing. This
provides input to the control module in
the electrical cabinet connected to a
touchscreen for the operator interface.
The control module analyzes the relative
pull forces on each production bend
cycle relative to a learned reference and
programmable tolerances, displaying the
results on the operator touchscreen. If
a bend is within tolerance it passes and
the process continues. If it is outside of
tolerance the process variance is indicated
and the process can be interrupted as
required.
The PVM bend monitor will catch a broken
mandrel due to sudden excessive tension
or as a result of a fatigue break. Stopping
the process when a mandrel fault occurs
allows removal of the defective part, and
prevents production of additional scrap
material or possible collateral damage to
equipment. Figure 3 shows a production log
file from the monitor indicating a mandrel
fault during the first bend in a four bend
part, and subsequent recovery to steady,
stable production after repairs.
In monitoring the mandrel pull force through
every bend cycle without adding time or
processing steps, the PVM2000-MB™
mandrel bend monitor provides an alert to
potential issues before they become real
problems.
This pro-active system measures the
process variance on a machine for
every cycle of production, detecting
problems at source, often well before they
become quality issues. Early detection
of a degrading process reduces scrap,
and saves unnecessary downtime and
machine repair.
OES Inc
– Canada
Fax
: +1 519 652 3795
:
oes@oes-inc.comWebsite
:
www.oes-qualityassurance.comtube bending machines
tube end forming machines
automation systems
tube cutting machines
tube cleaning systems
We produce:
www.transfluid.de
Figure 3 – A production log file from the monitor indicating a mandrel fault
Figure 4 – The PVM2000-MB™ mandrel
bend monitor from OES