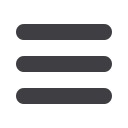

92
›
I
nspection,
M
easuring,
T
esting &
M
arking
M
ay
2009
have no affect on the measurement. The
combination of 1-6 laser/camera modules
allows the measurement of virtually all
shapes, achieving an optimal measurement
result with the smallest possible number of
laser/camera modules.
The Odac Trio system is based on
Zumbach’s vast experience, gained over
many years of design and manufacture
of optical diameter gauges. This
measuring head features 3 integrated
measurement axes.
Conventional 2 axis instruments with laser
or CCD can only provide approximate
values for a minimum OD and maximum
OD and ovality. The mean value (X+Y/2) is
influenced by the orientation of the product
ovality within the measuring field.
Advantages of the ultra-compact Odac Trio
include 3 synchronized measurement axes
on 1 single plane, and reliable detection of
out-of-round condition, regardless of the
orientation of the product ovality.
The device detects any deviation from
roundness of oval and out-of-round with
polygonal shape (multi-lobe), with highly
accurate yields regardless of the orientation
of the product ovality.
The Trio computes accurate values of
circumference and cross section, which
is important when mixing the products of
tube and hose. The technology also offers
increased measurement accuracy and
reliability, and integrated fault detector
with 3 times higher detection certainty and
sensitivity (than 2 axis models).
Zumbach Electronic AG
– Switzerland
Fax
: +41 32 356 0430
:
sales@zumbach.chWebsite
:
www.zumbach.comThe machine can be used with oscillating
gauges for round and non-round products
(flats, squares hexagons etc). This system
has up to 6 measuring axes for seamless
360° coverage, with measurement
independent of twist.
There are no blind zones, with cross
section computation and oscillating or static
operation. The version with
static gauges is especially
suited to round products.
This compact system has up
to 6 fixed axes, no moving
parts and an extremely fast
measuring rate, with short
measuring distances.
Steelmaster gauges offer
decisive advantages for
easy integration, dependable
operation and data processing
and display. They include
hi-tech laser scanners with
high accuracy, up to 6,000
measurements (1,000 per
scanner), compact industrial
PC, and highly developed
software. In addition, the
Steelmaster comes with sophisticated
mechanics and protection system, and close
to zero maintenance.
Designed for any requirement, the modular
Profilemaster system provides accurate
inline profile measurement using the ‘light
section’ principle and machine vision. One
or up to six laser/camera modules measure
the cross-section of the moving profile.
A
powerful
PC
based
processor adds together the
partial pictures of the cameras
made up of straight lines and
radii to yield the momentary
cross-section of the profile.
All relevant dimensions such
as width, height, angle and
radii are combined to form the
full cross-sectional picture.
The nominal values for the
profile can be directly imported
from the CAD construction
(as a DXF file), which allows
easy and problem free
programming.
Changes in speed and
twist within normal limits
Zumbach
Electronic,
Switzerland,
provides a complete line of measuring and
monitoring instruments. Typical applications
of these systems are hot rolling mills for
wire steel rod, profiles and seamless pipes,
welded pipe production, test stands (NDT),
and cold processes, like peeling, grinding,
straightening, and polishing.
This technology is geared towards closer
tolerances (½, ¼ DIN), zero faults, 100
per cent quality control, higher productivity,
faster startup, less downtime and
manpower.
Zumbach provides three systems groups:
Steelmaster, Profilemaster
®
and Odac
®
Trio. Steelmaster is a non-contact laser
measuring system range for hot and cold,
inline and applications in rolling mills.
Profilemaster provides profile and shape
measuring systems for hot and cold, inline
and offline applications, while Odac Trio are
3-axis laser diameter gauges.
Steelmaster gauges and systems are based
on the latest technology. Almost 300 units
are in operation in hot rolling and similar
processes. They are backed up by many
thousands of Odac scanners, operating in
cold processes.
The Steelmaster processor is the ‘brain’
of the system. It processes the measuring
data, communicates with the plant
network and provides the operator with
self-explanatory displays and key data.
The process transparency is dramatically
improved, especially if multiple measuring
heads are installed.
All-round capability for non-contact inline
dimensional measurement
The Profilemaster measuring unit
The Steelmaster non-contact laser measuring system