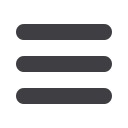

98
›
I
nspection,
M
easuring,
T
esting &
M
arking
M
ay
2009
The number of process cards required has
been reduced by half, and data security
is now virtually guaranteed with the
introduction of a RAID hard-drive backup
system.
An Inspectech ultrasonic skelp monitoring
system was recently commissioned at a
new tube mill in Mexico.
The system was ordered to allow the mill
to inspect strip materials for OCTG to the
latest specifications of API and ISO. Recent
updates to these inspection standards have
generated new enquiries for the strip testing
system.
InspecTech has provided flaw detection
systems for the tubular goods industry,
using eddy current, flux leakage and
ultrasonic technologies in both online
and offline applications for North
American and international markets
since 1977.
Inspectech Analygas Group
– Canada
Fax
: +1 416 757 8096
:
sales@inspectech.caWebsite
:
www.inspectech.caStrip and plate inspection systems are
custom designed for material inspections
up to 6.4m wide and 100mm thick, with
operating temperatures up to 200°C.
These ultrasonic systems are suitable for
thickness monitoring, lamination detection
and
surface
flaw
detections.
Inspectech
has
recently updated and
redesigned its skelp
monitoring systems.
The
mechanical
system has been
enhanced to allow
every
transducer
more
positional
adjustment.
The
computer-based
electronics
have
been re-packaged to
a reduced format by
implementing new back-
plane technologies.
Inspectech Analygas Group, Canada, has
supplied customised NDT solutions for the
tube and pipe industry for over 30 years,
and continues to explore new technologies
and innovations to meet the industry’s
NDT needs.
• SIDE LOADING FOR FAST TOOL
CHANGES AND NO LIFTING REQUIRED
• Infinitely adjustable
expansion & reduction
• P.L.C. control -
300 program memory
• High production
capability
• No tube clamping
required
• End form on or
near bends
• High quality build with
practical platforms
• Full 2 year warranty.
Unit 24, Padgets Lane, South Moons Moat,
Redditch, Worcestershire B98 0RB, England.
T: +44 (0)1527 518520 E:
info@avamatic.co.ukW:
www.avamatic.co.ukGermany: Tel: 02150 2500
Netherlands/Belgium: Tel: (04756) 6888 USA: Tel: 708 272 7880
£7,900
+VAT
FROM
ONLY
NEW AV65S
TUBE END FORMING MACHINE
Inspectech’s skelp monitoring system has been commissioned at a new tube
mill in Mexico
Meeting demands for thorough strip and
plate testing in modern pipe mills