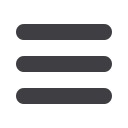

94
›
I
nspection,
M
easuring,
T
esting &
M
arking
M
ay
2009
traceability through a built-in data logger,
which records minimum and maximum
thickness readings across the weld area
and strip thickness.
GE Sensing & Inspection
Technologies
– UK
Fax
: +44 1727 795400
:
david.jervis@ge.comWebsite
:
www.geinspectiontechnologies.comThe transducer test head
then uses its phased
array elements to monitor
the inside and outside
diameter of the weld
as it is being cut, at a
scanning rate of up to
300 profiles/sec.
Transducers and shoes
are available to monitor
tubes from 50mm up
to 500mm in diameter.
Typical
coverage
is
±25mm from the nominal
weld centre line.
Inspection data is dis-
played in a true-to-scale
cross-sectional profile at
one or multiple monitor
screens. High and low
limit alarms provide warn-
ing of weld profile devia-
tion. Intelligent dynamic
software averaging tech-
niques minimize the pos-
sibility of false readings.
The
weld
profile
visualization
system
features
all-
electronic setup for simplicity and
repeatability. It can be installed within feet
of the weld station, depending on local
temperature and geometrical conditions.
It thus operates as a process control
system and a quality control system.
The system can be combined with
flaw detection and it allows inspection
GE Sensing & Inspection Technologies
has introduced an ultrasonic weld profile
visualisation system that uses phased array
technology.
This new scarf monitoring system
provides an accurate picture of both the
ID and the OD profiles of scarfed ERW
pipes.
The online system operates in real-time
to monitor scarfing as it takes place
during the manufacturing process. As
a result, it is possible to effect real-
time control of the scarfing process by
identifying events such as tool drift and
edging as they occur. This can achieve
significant reductions in scrap.
The heart of the new system is the
ultrasonic phased array transducer, which
electronically simulates the scanning
action required to provide the weld profile
information.
The resultant signal is then fed into the
field-proven UTxx digital flaw detection and
thickness measurement system.
This process incorporates standard or
phased array flaw detection channels and
all the associated processing electronics.
It ensures a complete scarf monitoring and
flaw inspection package.
In operation, the transducer test head
assembly is mounted in such a way that
it is directly above the weld line. The mill
coolant acts as the ultrasonic coupling
medium.
AGR Field Operations, USA, specialises in the design and
manufacture of state-of-the-art ultrasonic data acquisition
equipment. AGR combines phased array, ToFD and pulse/echo
into a convenient and powerful range of instruments designed to
suit the widest range of applications.
AGR’s product range includes the 8-channel miniature TD Pocket-
Scan and 16-channel TD-Scan with motion control. This device
offers ToFD and pulse/echo in various forms. The company’s
range also includes the TD Handy-Scan and TD Focus-Scan with
8 and 16 conventional channels respectively for ToFD and pulse
echo, together with 64/32 and 128/64 phased array respectively.
The TD Focus-Scan also boasts built in motion control.
The company’s latest advanced ultrasonic system is the
TD Handy-Scan, a fully portable multifunction instrument
with both phased array and conventional channels. It
provides a compact, versatile instrument ideal for field use in
petrochemical plants, offshore installations, and power station
workshops.
The TD Handy-Scan is supported by AGR’s latest tried and tested
version of the TD-Scan software incorporating TD Super-View.
The latest TD-Scan software has been enhanced to provide
the operator with superior one-handed control of the handheld
instrument and ASME code compliant features.
AGR Field Operations
– Norway
Fax
: +47 56 31 60 01
:
utsales@agr.comWebsite
:
www.agr.comNew phased array scarf monitoring system
The ultrasonic weld profile visualisation system uses phased array
technology
State-of-the-art ultrasonic data acquisition equipment