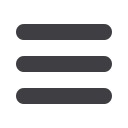

90
›
I
nspection,
M
easuring,
T
esting &
M
arking
M
ay
2009
Unseen, unknown, and unresolved
process issues in mandrel bending lead to
premature tool wear, unexpected equipment
damage, and costly downtime. Even worse,
undetected mandrel faults or poor quality
parts can be produced and shipped without
any realization of a quality issue. Current
QA practices may not be adequate.
Detection of a broken mandrel link is
critical, so manufacturers try to have some
system in place to verify the presence of
the intact mandrel. However, even when
these systems are successful in detecting
a broken mandrel, they do nothing to alert
the operator ahead of time of a process
change that could result in either a broken
mandrel link, or the production of poor
quality parts.
A different approach to quality is to
use an in-process monitor to capture
the ‘signature’ of the process. It is then
possible to compare the signature of
each production cycle with a reference of
known good parts as a way to monitor the
manufacturing process. This is known as
process variation monitoring, or PVM.
The fundamental theory behind PVM is
simple: if a process (including inputs,
force, and tooling) is known to be capable
of producing only good parts, and the
process is consistent and repeatable, then
the output of good parts should also be
consistent.
If any of these process variables change,
such as raw material (ie thickness,
hardness), lubrication, tooling condition,
and even machine condition (bearings,
clutches, setup, etc), the resultant signature
will change. An effective PVM system
detects the change and provides an alert.
Process variation monitoring represents
a necessary practice to detect broken
mandrel links or deteriorating quality
issues such as loss of lubrication, galling,
tube slippage, out-of-spec material, or a
change in material hardness that can lead
to breaks. The simple benefits include
reduced scrap and increased revenues,
elimination of unnecessary downtime, and
avoidance of repair.
Some vehicle manufacturers have specified
that an objective system be utilized to
‘see’ that the mandrel assembly remains
intact, leading some manufacturers to
focus attention on the mandrel with vision
detection or complicated mechanical
devices.
Initiating an effective monitoring system
requires examination of the entire process
www.transfluid.deProcess variation monitoring (PVM) in
mandrel bending
Figure 1 – Loss of lubrication
Figure 2 – Misalignment of the setup