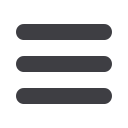

Technology News
www.read-tpt.com68
J
uly
2014
High-pressure tubes –
3,000 bar and above
THE Poppe + Potthoff Group provides a
range of products and services in high-
pressure technology. The company’s
seamless precision steel tubes are used
in hydraulic units, pressure test benches
and injection systems for diesel engines.
The company states that, thanks to a
special manufacturing method, its high-
pressure lines are considered to be very
safe.
Diesel injection technology has
accompanied the family-run business,
which was founded in 1928, for more
than 40 years. With high-carbon steels
E 355, PP 600 and the newly developed
PP 1000, three high-strength standard
materials are available for high-
performance lines. The autofrettage
systems and test benches specifically
developed by the engineering company
Poppe + Potthoff Maschinenbau GmbH
ensure the fatigue strength of the high-
pressure lines.
The company’s technology centre,
close to the precision steel tube mill in
Werther, Germany, develops customer-
specific solutions, such as double-
walled common rail systems for ships.
Prototypes can be made in just a
few days and validated as in series
production.
In
addition,
an
integrated
manufacturing plant was constructed in
Ajka, Hungary, in 2013. High-strength
tubes are drawn here and processed into
components under one roof. The flexible
processes that are optimised throughout
meet the highest requirements of
cleanliness in accordance with 0ppm
targets. Common rails and diesel
injection lines are manufactured in
series for system pressures up to 3,000
bar and beyond.
Poppe + Potthoff GmbH
– Germany
Fax: +49 5203 91 66100
Website:
www.poppe-potthoff.comExtrusion lines for pipes
AMUT manufactures line configurations
to extrude pipes, offering solutions for
several materials and diameters.
The range of production includes PVC
pipe lines with diameter of 16-1,200mm
for rigid pipes and 8-63mm for flexible
pipes; PE pipe lines (mono and multi-
layer) with diameter of 16-1,600mm;
and special pipes (multi-layer) such
as PE-X, PA (fuel pipe), PP with glass
fibre reinforced inner layer (hot water),
flexible PVC braided/reinforced hoses,
irrigation, foam core, corrugated, bi-
oriented and automotive pipes.
Focused on the needs of its
customers, Amut mainly develops
tailored lines and special equipment.
For example, the company delivered
in Vietnam an extrusion line for the
production of PE100 pipes with an
external diameter of 1,000mm. A
new compact extrusion die and an
extruder capable of reaching an hourly
capacity of 1,200kg were designed and
manufactured for this purpose. The die
is provided with 16-spiral distributors to
ensure wall thickness uniformity on the
whole pipe, while the extruder is based
on a bimetallic barrel and wear-proof
coated screw.
For the automotive industry, Amut
offers lines to produce multi-layer PA
pipes (up to five layers), which are
largely used to convey fuels or hydraulic
oils. These PA pipes feature good
flexibility, reduced water absorption, and
high resistance to low temperatures,
humidity, cracking and abrasion.
Through a continuous thickness
control and diameter adjusting system,
Amut lines ensure the quality of pipes,
even when frequently changing product
features and dimensions, at constant
production working conditions.
Amut extrusion lines are supplied
with gravimetric dosing units to keep
the layer thickness constant and to
control the size and weight of the pipes.
Plasticising units, barrels and screws
are all made of special alloys to ensure
resistance to abrasion and corrosion,
and their particular geometries are
essential to obtain high production rates
and homogeneous quality of the melt, at
low energy consumption.
The limited friction of the extruded
material in the sizers allows control
of the tension acting on the pipe, to
achieve high extrusion speed, such as
60-70m/min in the case of five-layer
pipe extrusion.
Amut SpA
– Italy
Fax: +39 0321 474 200
Email:
amut@amut.itWebsite:
www.amut.itCommon rail system with diesel
injection lines from Poppe + Potthoff
Amut manufactures a number
of extruded tube solutions