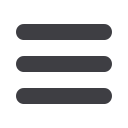

Technology News
www.read-tpt.comJ
uly
2014
73
Straight welded, lipped-end pipes and components.
ø 60 mm to ø 1600 mm in a standard range.
With pull-ring or flange connection.
Up to ø 400 mm normally dispatched immediately
from stock.
Powder coated steel or hot-dipped
galvanised steel as well as stainless steel.
1-3 mm wall thicknesses.
Larger diameters / special requirements upon
request.
Shock-explosion certified pipes and
components available.
Original Quality to a Modular Design
The
QUICK CONNECT
®
pull-ring makes
the acclaimed Jacob modular pipe system
even more economical for installation.
In new plants for animal feed, pharmaceuti-
cals, chemicals, food, glass, semiconductors
or environmental technology as well as for
upgrading existing layouts user-friendly
system installation becomes precise and easy
due to the great versatility of mass-produced
pipe components.
Request a new catalogue!
+49 (0)571 95580
or at
www.jacob-pipesystems.euFr. Jacob Söhne GmbH & Co. KG,
Germany
·
Tel. +49 (0)571 95580
www.jacob-pipesystems.euinstallation friendly
perfect fitting
shock explosion proof
easy expandable
QUICK CONNECT
®
EUROPE’S NO. 1 IN MODULAR PIPEWORK SYSTEMS
EC 1935/2004
plus FDA
514497_TubePipeTechnology_180x60_gb_4c.indd 1
24.04.14 10:47
Oil, gas and structural pipe mill
equipment
KUSAKABE Electric & Machinery,
based in Japan, is a pipe and tube
mill manufacturer that is continually
developing, innovating and improving
the design and manufacture of pipe and
tube mills for the international market.
From API, oil, gas and structural to
automotive and general engineering
applications, Kusakabe can supply
the whole mill or individual pieces
of equipment to meet production
requirements.
All of the equipment is designed and
built in Japan to exacting Japanese
standards and workmanship.
The forming section of the oil, gas and
structural mills is made up of an entry
guide, the Universal Forming section
followed by the patented Cassette style
fin pass section.
The Universal Forming section
includes the breakdown passes and
all the forming up to the fin pass
stands.
Size changes are fully automatic
and controlled by the motorised roll
positioning equipment in conjunction
with an HMI (Human Machine Interface)
screen with its menus and recipes.
The positioning of the rolls is driven to
the predetermined optimum position for
each product.
The forming section using universal
tooling requires no rolls to be changed:
the position of the rolls are adjusted to
suit all the diameters to be made.
The Kusakabe Universal Forming
is designed so that the strip is easily
visible as it makes its way through the
forming process. This makes it easy for
operators and engineers to see what is
happening in the forming process. The
forming flower used to shape the pipe
minimises the work hardening while
providing the ideal edge presentation for
HF welding.
Kusakabe Electric & Machinery
Co Ltd
– Japan
Email:
sales@kusakabe.comWebsite:
www.kusakabe.comManual and automatic
end forming machine
SMS Engineering manufactures manual
or automatic rigs for end forming,
flattening, swaging, calibrating, drawing
and flanging steel, copper, aluminium
and brass tube.
The machine is equipped with manual
loading and unloading but upon request
an automatic loader and unloader can
also be supplied.
Max tube working is Ø30mm, and
max wall thickness is 1.5mm.
The machine can work tubes that are
round, square, rectangular, oval or most
other shapes and it is equipped with a
hydraulic power pack, electrical cabinet,
protection and safety as required by CE
regulations.
Extra
options
include
air/oil
exchanger, lighting guard application,
nebuliser lubrication on the tooling each
time the cycle stars, and extra working
stroke.
Simultaneous working is possible at
both ends of the tube using one or two
tools on each head. The fully automatic
machine is equipped with bundle
loader, overhead manipulator and
complementary operations.
SMS Engineering Srl
– Italy
Email:
commerciale@sms-italy.itWebsite:
www.sms-italy.itThe automatic machine