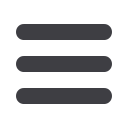

19
Chemical Technology • November/December 2016
Condition monitoring specialists, WearCheck,
has now extended their fuels, lubricants, air
and coolants (FLAC) maintenance programme
to include unique bypass filters, whichminimise
contaminants, thereby extending the life of the
oil and fuel.
The filters were initially trialled at a chrome
mine on three GHH machines running air-
cooledmotors. Once proven effective, the filters
were then fitted to a further 27machines in the
same mine. The mine has already recorded
savings of R1,7 million after paying for the
implementation of theWearCheck programme.
Also known as depth filters, the bypass fil-
ters are bolted externally on each component,
and the oil or fuel of that component passes
through the filtration system, similar to how
an individual dialysis machine would assist a
patient to filter their own blood.
The filters function best as part of a com-
prehensive condition monitoring programme,
and, following the successful trials, they are
being widely installed on different machines.
They are designed to clean oil and fuel used
in a variety of industries, including mining,
earthmoving, transport, construction, manu-
facturing, shipping, electrical and aircraft.
Fuel typically passes through three filters
– first the OEM water separator, next the OEM
diesel filter, and finally WearCheck’s depth
filter, which is last in line, and which provides
extremely fine microfiltration, screening par-
ticles between 0,5 and 1 microns in diameter.
The filters can either be fitted to existing
components or installed during construction
or rebuilding of the machine.
Chris Hattingh (operations/technical sup-
port for WearCheck), outlines some of the
advantages of the process, “By ensuring the
fuel at the injector tip in a diesel engine is
super-clean, it protects the moving parts and
keeps these within spec for much longer, al-
lowing for better atomisation.
“During the trial process for the filters, our
FLAC programme initially identified the correct
oil to be used for different components, and
outlined optimum cleanliness procedures for
bulk oil storage. The bypass filters were then
fitted and found to extend the oil’s longevity
and boosted the components’ life.
“The advantage of cleaner burning fuel
means more power. Because there are now
potentially fewer by-products passing into the
crank case oil, such as soot, the additive pack-
ages don’t have to work so hard, so they may
also last longer.
“By using scientific data on the oil’s condi-
tion, and knowing that the filters have cleaned
the oil or fuel effectively, we can advise custom-
ers when it is feasible to extend the oil drain
interval without risk, thereby saving them
money.” WearCheck celebrates 40 years of
condition monitoring excellence this year.
For more information
contact WearCheck on
Tel +27 11 392 6322 or +27 31 700 5460 or
www.wearcheck.co.zaor
FOCUS ON PETROCHEMICALS
WearCheck filters save money
Bolted externally onto the machine is one of
WearCheck’s bypass filters for the transmission.
The filters have already saved a mine over
R1,5 million during an initial trial process.
SA lubricant market gets the Royal Purple
treatment from Filter Focus
“Filter Focus is proud to be associated with Royal Purple, which offers the highest level of protec-
tion, while reducing friction co-efficiency and associated parasitic losses. With Royal Purple
lubricants significant energy saving can be gained.” - Chief Operating Officer, Filter Focus, Craig
FitzGerald. For detailed product information on the Royal Purple product range,
visit
www.royalpurpleoil.co.za.