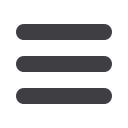

There are inefficient and costly flaws with the traditional approach of
engaging test engineering late in the NPI process. Engaging earlier in the
design cycle can lead to faster time-to-market, lower manufacturing cost,
and improved yield.
Many organizations have different business units for the develop/
deploy and support/maintain costs of a test system. Test engineers can
greatly impact the operational costs of supporting a system, but must
expand their influence beyond their own organization to understand and
implement solutions to mitigate the long-term costs of supporting an ATE
system.
field, your test cases are far more
inclusive than the “did we build it
right” manufacturing test case. You
will need to emulate the real-world
environment with highly synchronized
signal sources including closed-loop
control between the sources and
analyzers to stress the DSP engine
and measure the phase-coherency
of the system. To address the
synchronization and data transfer
challenges, test engineers need
to look beyond traditional boxed
instrumentation to a platform-based
approach such as PXI. To emulate the
real-world environment with closed-
loop control, engineers need flexible
RF instrumentation architecture
that combines data streaming
architectures, FPGA-based signal
processing, and high-performance,
high-instantaneous bandwidth RF
front-end technology to capture and
process the incoming pulses.
It’s also no secret that operational
costs are high when sending units
back to the intermediate- (I-)
or depot- (D-) Level centers for
maintenance or repair. As RF test
equipment becomes easier to adopt
in field test, these operational costs
greatly improve. Not only does
the organization benefit from the
decrease in operational cost, but they
can get better IP leverage between
the depot and field testers for in-situ
troubleshooting and diagnostics.
As you can imagine, the RF challenges
of scalability, synchronization, and
latency create complex system-
level test architectures for the test
engineer and are quite different than
replacing the legacy oscilloscope
and mitigating TPS rehosting costs,
though both technology elements
are great opportunities for the test
engineer to provide significant value
to the organization.
Increasing Sphere-of-Influence to
Reduce the Cost of Test
A third, and maybe more subtle, pain
point for test engineers is justifying
short-term spend to mitigate long-
term operational costs. Market
pressures are as high as they have ever
been, so test engineers are opting for
point-solutions that neither provide
the scalability for evolving technology
demands nor have an architecture
that simplifies maintenance for future
upgradeability.
Furthering this problem is the fact
that this short-term spend may
not actually come directly from the
test engineering budget. Looking
upstream, we all know how difficult
it can be to get a design engineer
to modify a design once it meets
the design specifications, but
organizations can see significant
improvements to their bottom line by
engaging the test engineering group
early as part of a Design For Test
(DFT) or Design for Manufacturability
(DFM) strategy. When yields improve
and asset utilization increases, these
optimizations typically go directly to
the gross margin of the product.
Beyond DFM, it’s also critical that
the test engineers be involved early
in the new product introduction
(NPI) process. By actively engaging
in every stage-gate of NPI, the test
engineer can be developing product-
24 l New-Tech Magazine Europe