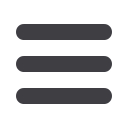

55
products in the broadest sense of the term. Its voyages are always upstream, to fixed
destinations like Karlsruhe and Basel. The company’s ships often navigate canals too.
For example, Bottrop/Gelsenkirchen, which has a maximum air draft of 4.20 metres.
It didn’t take long for the conversation to turn to Rensen-Driessen’s Moneymaker
tanker. The most obvious competitive advantage offered by a 110.00 x 11.45-metre
ship was the shallow depth of 4.65 metres in the case of an air draft of 4.20 metres
(with ballast). In the case of a draught of 3.20 metres, the eight tanks have a joint
capacity of 2,638 tons. However, even when the draught is limited to 2.80 metres
(for example), a Moneymaker is still able to boast a capacity of 2,170 tons. One of the
secrets of its success is the fact that it has eight tanks rather than the 10 customary
on other vessels. This saves steel, keeps the weight of the ship down and yields
cargo-related and fuel advantages too.
The brother and sister were very interested and the next step led to the identification
of some changes that they wanted, which were then incorporated in detail in
drawings and in the calculations below. If the build-plan was given the go-ahead,
Rensen-Driessen Shipbuilding would be able to deliver the ship to them on a turnkey
basis. The hull would be delivered by S.C. Santierul Naval Orsova S.A. as per the
design agreed on, while outfitting would be completed by Dolderman B.V., a company
based in Dordrecht in the Netherlands.
Armed with the build-plans and a positive operation-calculation for the first several
years, the family arranged an appointment in April to see a German banker that they
had been able to rely on for decades. The approval needed was gained, contracts were
signed and an exciting time started for Donald, Renate and their partners. Renate’s
partner produces designs and is involved in engineering in the field of maritime-
shipping electronics. Renate and Donald’s wife Annemarie sat down to decide on the
layout of the ship and spent many enjoyable evenings discussing all kinds of plans.
During the build, the family visited Orsova three times, the last of which was on 19
August 2016, to witness the launching of the ship and attend its naming ceremony.
The ship was named after the mother of Donald and Renata, who died at a young age.
The hull arrived at Dolderman’s premises on 29 September 2016. ‘This marked the
start of a huge outfitting process’ says Donald. ‘The company had everything it
needed in Papendrecht to make the project a success’ he adds immediately, telling us
briefly how happy he was about Dolderman’s outfitting work. Nothing was too much
for the Dolderman team that worked on their ship. There were no surprises, we were
consulted about everything and we were always able to speak to the same people.
Everything was always just as it should be, right down to the very smallest detail.
Donald gives an example: the fixtures for deck lighting. There was no need for us to
paint anything ourselves; everything was fitted in stainless steel as standard. There
weren’t any DIY jobs left for us to handle anywhere else on board either: Dolderman
provides turnkey delivery in the strictest sense of the term. Delivery and the first
voyage both took place at the end of December 2016.
When we ask them what they think after having used the ship for three months, their
answer leaves no room for doubt: ‘we are really surprised how well the ship handles’.
We got far more than we had expected. The ship delivered to us is above and beyond
what we were promised. The ship handles reliably and manoeuvres flawlessly. We are
very pleased with the engine rotation speed and fuel consumption too. Where we
used to use 210 litres of fuel on trips and voyages in our previous ship, we use just
160 litres today. The savings that we are able to achieve really stack up when you
consider them over the space of a whole year. This includes the time saved thanks
to rapid ballasting (jets) and unloading (up to 1,000 m3/hour). ‘However, these time
savings are at the expense of our crew’s downtime’, jokes Donald.
To summarise, Meeuwisse Binnenschiffahrt GmbH is very happy about the entire
experience. ‘It was a successful investment for the family and we would definitely
opt for the same parties if considering a new build again in the future’ say Donald
and Renate.